Date: November, 2023 | Category: Quality | Author: Hana Trokic
While “going green” may be a proud point for many businesses in this day and age, in the world of packaging and design, it’s not necessarily going far enough. Instead, it’s all about being sustainable.
However, true sustainability doesn’t just take into account the materials that go into packaging. True sustainability also considers potential waste during the production process. When introducing end-to-end sustainability, businesses need to look back to the very beginning, to the point where the packaging is designed and then approved.
It is important to note that the packaging approval process can result in many rounds of revisions until everything is ready for production. The result can create wasted resources if your process isn’t as tight as possible, even if the packaging itself is 100% sustainable.
As a result, significant resources get wasted when mistakes slip through your supply-chain cracks. Avoidable errors can result in recalls leading to heaps of wasted packaging that have no value. For perspective, in 2015 alone, 77.9 million tons of municipal solid waste generated in the United States consisted of containers and packaging. Over one-third of that total ended up in landfills.
Read on to discover how to create truly sustainable packaging and processes for your business.
What Is Sustainable Packaging?
While a product that’s labeled as “green” carries a positive, eco-friendly connotation, it’s vague by standards set by the Federal Trade Commission.
For example, “green” generally means one or some combination of the following:
- Compostable
- Degradable
- Non-toxic
- Ozone-safe/ friendly
- Recyclable
- Made from recycled content
- Made with renewable energy
- Made with renewable materials
- Refillable
“Green” may sound satisfactory, but each of the above actually conveys something tangible. According to Diana Fryc, Director of Operation of Retail Voodoo, using compostable packaging is just one step.
“Aside from compostable packaging, there is still a strong desire to reduce the size of packages, continued desire to use fewer adhesives, and continued use of the post-consumer recycled material,” she says. “Lighter materials to save on shipping costs and form factors that maximize shelf space bottles will also continue.”
In fact, packaging that’s “sustainable” is understood to meet a long list of specific criteria, featuring many of those same characteristics. To further illustrate this point, the Sustainable Packaging Coalition has developed its own criteria for what defines sustainable packaging:
- Sourced from materials that each remain healthy throughout the lifecycle
- Manufactured using clean technologies and best practices, to optimize materials and energy, thereby meeting/exceeding competitive performance and cost standards
- Transported efficiently via fossil fuel alternatives, helping to develop renewable energy markets
- Recycled, recovered, and utilized in closed biological/ industrial loop cycles
Of course, the International Organization for Standardization (ISO), the Consumer Goods Forum, and CEN all have alternative packaging standards. So, globally speaking, there aren’t any hard, fast rules for what constitutes sustainable packaging. There are, however, certain guidelines.
Following them is far from easy, but this guide will help you understand the basics as you maneuver through the complex world of sustainable packaging and its implementation.
Reducing Your Carbon Footprint
Ultimately, by introducing sustainable packaging into your supply chain, businesses are aiming to reduce their carbon footprint as a whole. This includes securing product packaging workflow through effective quality control.
Preventing recalls by catching errors means less packaging, less waste, and therefore, a lot less energy consumed. After all, the resources needed to carry out recalls, which cost on average $10 million in the food industry, don’t include the transportation and labor costs of putting more packaging through your supply chain and re-shipping the product. It all affects your bottom line and the packaging footprint you’re trying to market as sustainable.
Therefore, it’s time to start looking beyond the product and at the complete end-to-end process. Many companies are integrating new technologies and automated systems that can spot errors before going to print as a pre-emptive strike against recalls. The main goal is to address sustainability, as it’s important to consider how products are made and how to be as efficient as possible with the resources available.
It turns out the idea that integrating sustainable packaging leads to higher costs is actually a myth. Studies show that companies that look to become more eco-friendly overall enjoy as much as an 18% return on investment increase. That’s potentially a lot of green for going green.
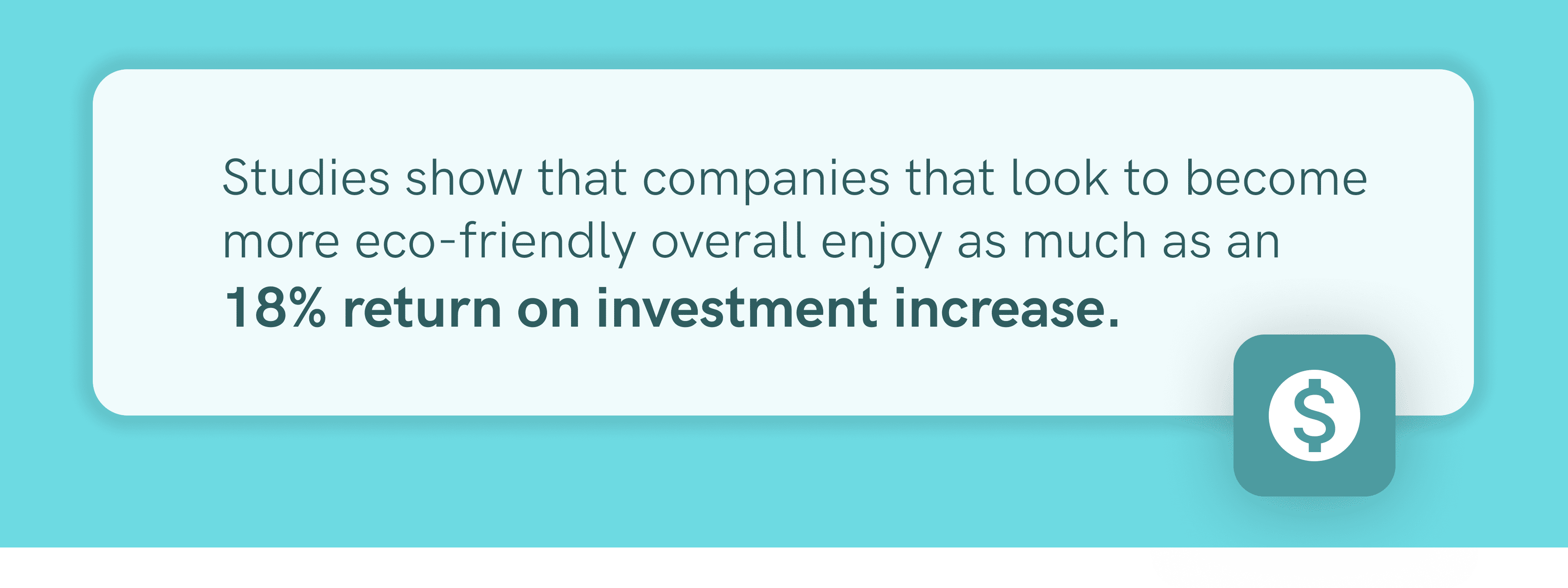
Have you heard about footprint packaging? Learn more by reading our detailed blog post.
The Need for Sustainable Packaging
There’s little denying the benefits of sustainable packaging. There are financial benefits in store for any corporation moving in that direction. That’s not just due to the increased back-end efficiency and economies of scale that result from such a move.
If marketed correctly, sustainably packaged products have been proven likely to sell more.
Obviously, a company shouldn’t make the switch simply to appease its conscience. All things being equal, it just makes sense to waste less and promote a brighter future filled with less waste.
“Packaging is a polluting factor” says Andreas Kioroglou, the CEO of Matador Design. “Creative design will [start to] take into account factors like the reduction of the carbon footprint of packaged goods throughout the supply chain and designs that will extend the packaging life cycle.”
Read what more experts are saying about sustainable packaging here.
Over the long term, it is expected that sustainable packaging solutions will lead to higher profits relative to one’s current process. The only thing holding companies back is the inevitable, albeit short, discomfort that results from transitioning to a new and improved process.
Implementing Sustainable Packaging
Packaging plays a crucial role in influencing customers’ buying behavior, yet unsustainable packaging can damage the reputation of a company, causing customers to switch to other brands that employ environment-friendly materials and processes.
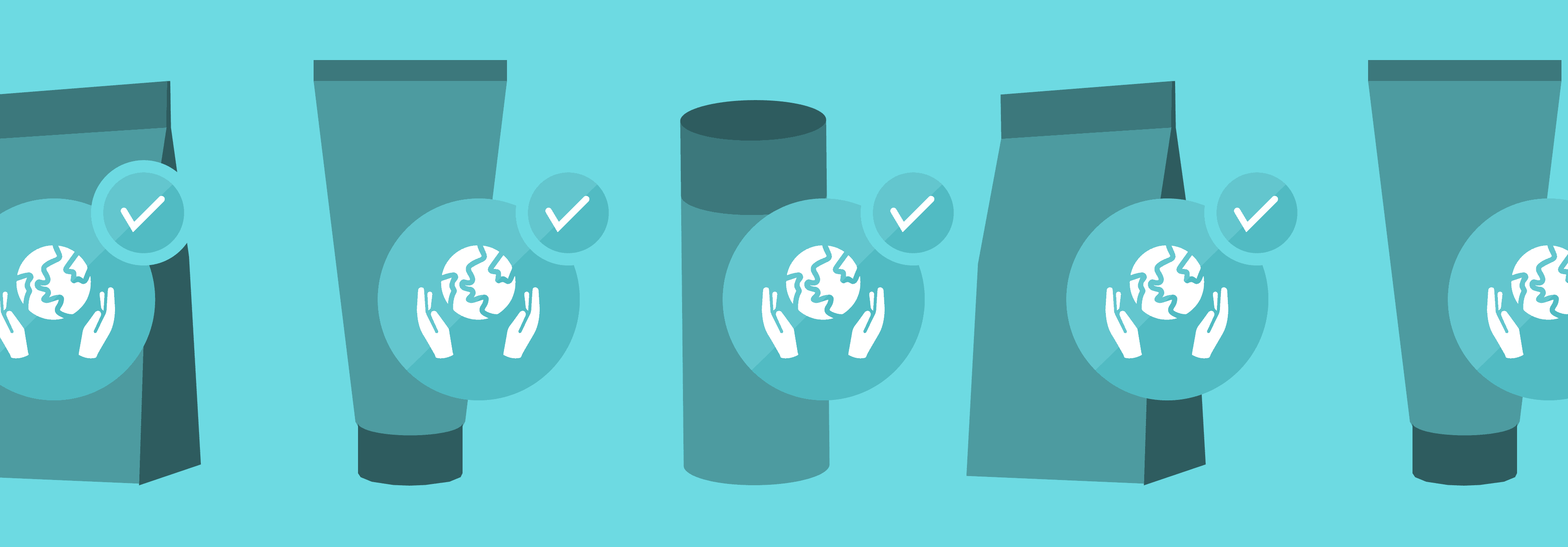
Unsustainable packaging is detrimental to the environment as it increases the amount of waste that is diverted to landfills, causing increased greenhouse gas emissions.
Sustainable packaging can reduce our ecological footprint at all stages of the product life-cycle, helping the manufacturer and the customer work towards a sustainable future.
With sustainability being the major agenda for almost all countries around the globe, several organizations are introducing sustainable packaging in order to reduce the negative impact on the environment and differentiate themselves from the competition.
However, the industry is not devoid of misconceptions that could cause confusion, making it challenging for organizations to work toward a sustainable future.
Sustainable Packaging Is An Added Cost
It is a common belief that a majority of product improvements come with a high price tag. Though the cost of sustainable packaging may seem to be high initially, it offers numerous benefits that contribute to the long-term success of a business. Moreover, socially responsible businesses incorporate the extra cost of sustainable packaging as a part of their business plan, assuring them of profits in the long term.
Adopting sustainable or green packaging enables marketers to connect with their eco-conscious and green-aware consumers, giving them a competitive advantage and boosting profits. In fact, studies conducted by the Carbon Disclosure Project (CDP) prove that organizations that adopt eco-friendly materials and processes are likely to see a return on investment of 18 percent or more.
Apart from attracting new customers and boosting your corporate image as an environmentally-responsible organization, sustainable packaging also offers innovative designs that can be tailored to the clients’ specific requirements.
For instance, waste can be recycled using the paper molding process and converted into customized packaging in order to meet the firm’s requirements for heavy and delicate products at an extremely affordable rate. All this eliminates excessive packaging, making the shipments light and drastically reducing the products’ footprints on the store shelves.
Additionally, in recent times, brands cannot afford to ignore eco-friendly strategies. Consumers increasingly prefer products that protect the environment, reduce global warming, and prevent air and water pollution.
Consequently, both emerging and advanced markets are drifting towards ethical and environment-friendly options, pushing designers, marketers, and package development experts to meet the right social and environmental standards.
Most countries also offer special subsidies and incentives for businesses that are looking to join the sustainability bandwagon. Moreover, firms going the sustainable way also enjoy preferential terms and tax rebates from the state and local authorities for setting up an environment-friendly business.
Thus, green packaging actually stands to save money by reducing material and shipping costs and minimizing waste, playing a persuasive role in helping customers choose your brand over the competition.
Sustainable Packaging Choices are Limited
With the growing concern regarding waste being diverted to landfills and the ensuing greenhouse emissions, customers are expecting firms to use eco-friendly elements in their products.
Consequently, packaging firms have come up with several innovative and green materials, namely polylactic acid (PLA), bagasse, recycled paper, and post-consumer polystyrene that can be used to manufacture coffee cups, plates, cutlery, and boxes.
For instance, Evocative, a New York-based biomaterials firm developed a mushroom-based material that can be used as an alternative to plastic packaging. Similarly, Biopac, a UK-based bioplastic developer uses polylactic acid (PLA) from renewable plant sources to manufacture compostable cups and food packaging.
Sustainable Packaging Adds to Waste
Sustainable packaging is not merely about the eco-friendly nature of the final product. Instead, it means that the packaging material is made from biodegradable, reusable, and environmentally-safe matter and uses energy-efficient manufacturing procedures and health-friendly working conditions for the staff involved.
Sustainable packaging helps firms streamline the packaging design, eliminating unnecessary material from the processes and creating less packaging-related waste. Materials such as biodegradable plastics, plant-based plastics, and recycled products are used to develop sustainable packaging, making it possible for manufacturers and consumers to reduce the amount of waste being diverted to landfills and the ocean floor.
For instance, molded fiber products, namely egg trays, fruit-and-vegetable trays, compostable plant holders, and wine shippers are made using biodegradable waste procured from recycling companies and individual households.
Sustainable Packaging is Unappealing to Consumers
Most commonly, when people think of sustainable packaging they envisage a dull brown or cream paper with visible reused fibers. However, technology has made it possible for design firms to come up with innovative packaging that harnesses powerful aesthetics and is environment-friendly at the same time.
Many international brands and powerhouses such as Samsung, Zara, and Puma offer attractive packaging yet use 100 percent eco-friendly material, preserving the planet and its natural resources.
Want to learn more about sustainable packaging myths? Click here to read our in-depth blog post.
Transitioning to Sustainable Packaging
While some companies are already fully onboard the sustainable packaging bandwagon, others are either on route to making the transition or have yet to make a firm decision on the matter.
For the companies already in existence, it’s about altering the course. Once you’ve committed to making the leap, it’s important to determine your ultimate goals. While the Sustainable Packaging Coalition’s criteria favor a circular economy (or closed loop, which relies on renewable energy), it’s by no means the only choice.
Another is to develop packaging with a linear lifecycle. There, packaging ultimately ends up as trash instead of biologically degrading. It can also be considered eco-efficient, depending on other production factors. It also means bigger short-term gains. The closed loop means more risk and long-term investment, but a higher potential payoff through legitimately sustainable packaging.
Here are some tips to help execute a proper sustainability strategy:
- Get buy-in: Empower employees to take charge and get more emotionally invested in the outcome of the change in strategy. Businesses can also get buy-in from the public. Communicate the change in your corporate philosophy. Done right, it can only improve your image as a forward-thinking company.
- Choose the right materials: It goes beyond selecting materials that are recyclable or even materials that are renewable. While renewable feedstocks are one sustainable direction in which to go, there are other things to consider. For example, how their functionality compares to that of traditional materials. “Sustainable” is great, but it means little if the packaging doesn’t do what it needs to.
- Get to designing: It will be a long process, but thoroughly evaluating each required packaging component will go a long way toward ensuring an overall sustainable design. Simple ones, made from single materials without secondary and tertiary packaging, are easily disassembled and recyclable. That also means minimal glue when possible. Creating packaging that is reusable and multi-functional also wins market points from a sustainability perspective and with consumers.
- Invest in quality control: Quality control processes are critical, especially when rolling out dramatically different packaging that can contribute to product spoilage. Automating quality control and eliminating proofing fatigue, human error, and errors in general, can also contribute to long-term sustainability.
Automation to Sustainability
Automated quality control tools are indispensable assets for businesses striving to enhance their sustainable packaging processes. These tools, driven by cutting-edge technology offer multifaceted advantages that extend far beyond mere error correction.
In the context of sustainable packaging, precision is paramount. This software meticulously scans through all packaging-related content, including labels, product descriptions, usage instructions, and promotional materials, ensuring that they are free from spelling, grammar, and formatting errors. By maintaining a high standard of accuracy, businesses reduce the likelihood of recalls, reprints, and costly product corrections, directly contributing to a more efficient and eco-friendly production process.
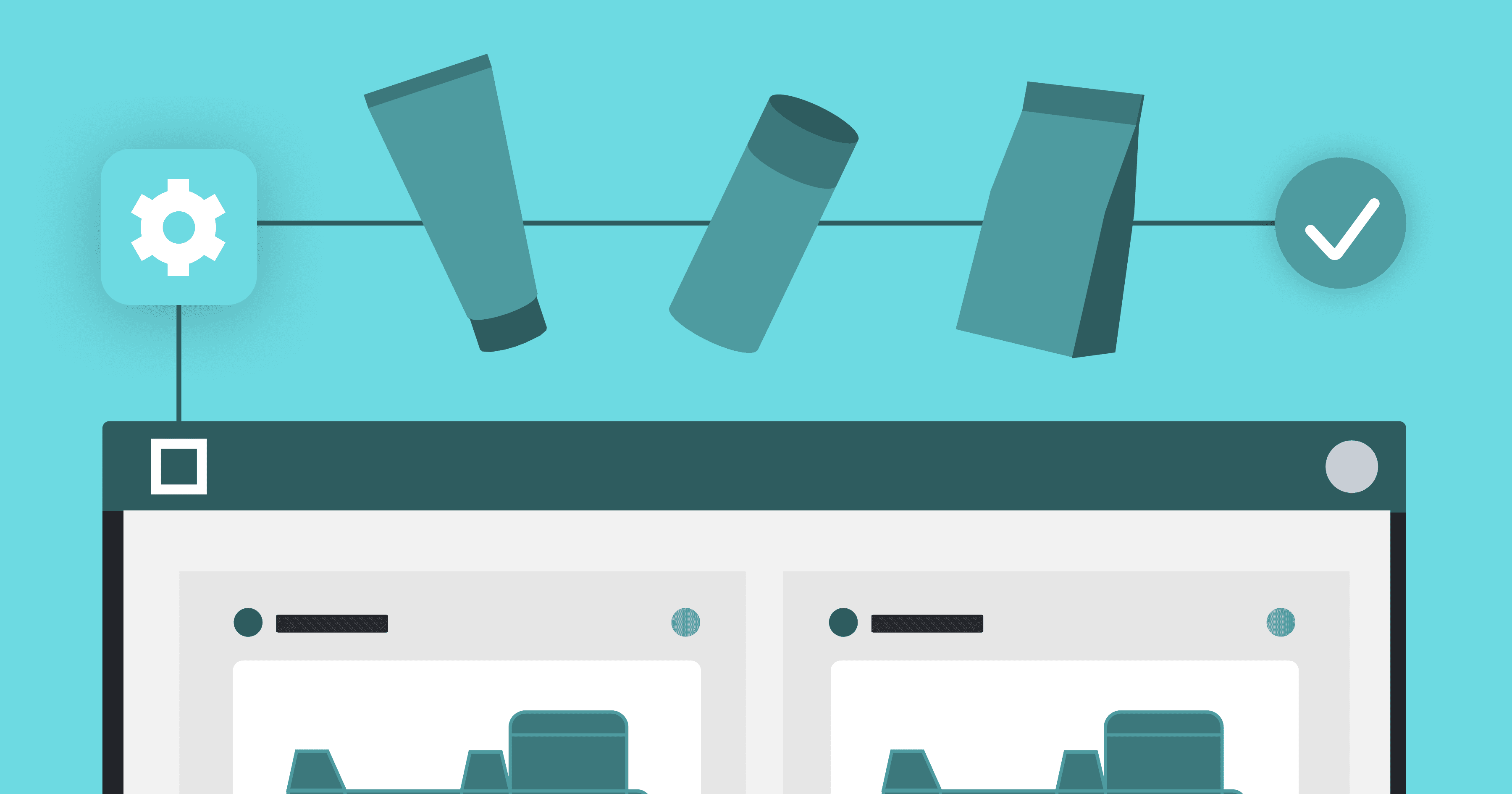
By preventing errors, reducing rework, and promoting sustainability, automated proofreading software helps minimize waste in the production process and optimize resource utilization. They aid in curbing the overuse of materials and energy while contributing to the reduction of the carbon footprint associated with packaging.
In the eyes of environmentally-conscious consumers, these efforts resonate as a genuine commitment to sustainability, ultimately enhancing a company’s brand reputation and its competitiveness in the market.
Automated quality control is not just about catching typos; it’s a vital enabler in a business’s journey toward sustainable packaging. The software streamlines operations, reduces costs, encourages green thinking, and helps businesses establish themselves as responsible actors in environmental protection and sustainability.
As sustainable packaging gains increasing importance in today’s eco-conscious world, this technological solution is becoming an indispensable instrument for companies committed to both excellence and environmental consciousness.
A Sustainable Future
The global packaging and protective packaging market was valued at $1.0 trillion in 2021, and is projected to reach $1.5 trillion by 2031, which would result from steady year-over-year growth.
Innovation will logically end up being one driver of that valuation, just as it is currently in the manufactured goods sectors directly reliant on it. That’s simply the nature of a free-market economy in which consumers reward the cutting-edge.
As a result, it’s no longer a matter of going green. It’s arguably not even about going sustainable. It’s about striving to reach sustainability. As the exact definition of “sustainable” is a fast and moving target, it’s more a matter of taking steps towards attaining that goal.
In a period of just three years, the number of firms listed on the S&P 500 that included sustainability issues in their Securities and Exchange Commission filings increased from 5% to 25%. That in and of itself may not be a testament to how successful sustainability can be, but it is of how the times are becoming more eco-friendly.
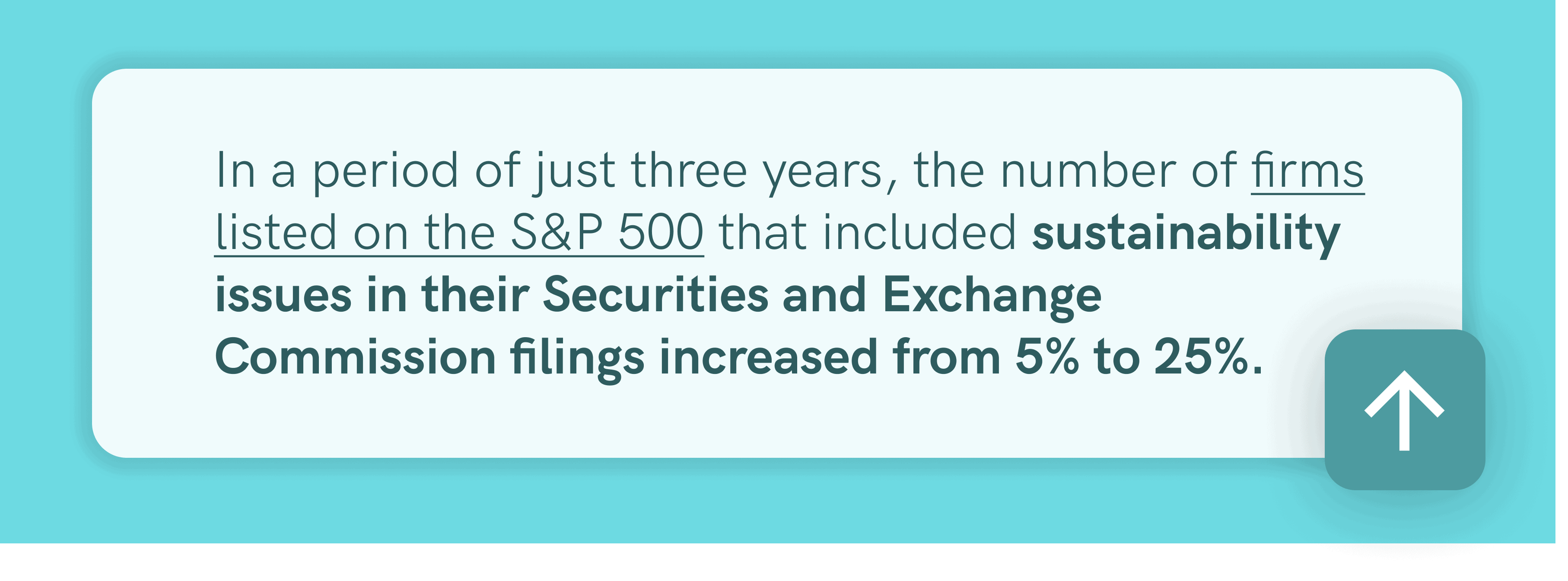
Joining in on the success means changing with the times, or, perhaps more accurately, adapting. Both customers and the companies behind the products they consume stand to benefit from the large-scale evolution of packaging, which is taking place right before our eyes.
If you would like to take a step into implementing sustainable packaging into your business, start by implementing smart, technological solutions that can easily help you get there. Automated quality control is a comprehensive solution that will not only streamline your proofreading and quality assurance processes, it will also help your business achieve true sustainability with far greater ease.
Request a demo of our innovative proofreading software and see how this technology can revolutionize your every day, sustainable business practices.
Medicine Packaging: Navigating Regulations in the UK
Date: January, 2024 | Category: Compliance | Author: Hana Trokic
In the UK healthcare industry, medicine packaging plays a crucial role in ensuring the efficacy and security of not only medical products but of consumers as well.
Over the years, requirements of UK medicine packaging have undergone significant changes, driven by advancements in technology, changes in consumer expectations and needs, and, most importantly, the ever-evolving stringent regulations imposed by regulatory agencies such as the MHRA.
Understanding and navigating these regulations is essential for medical companies to bring their products to market quickly and securely, and for healthcare professionals to ensure patient safety when prescribing medicine.
The Early Days of UK Medicine Packaging
Throughout history, the main role of UK medicine packaging has been to safeguard and conserve the contents of medical products. Glass bottles and vials were commonly used and were typically sealed with cork stoppers.
These bottles were usually accompanied by simple labels containing essential information. The labels were essentially handwritten instructions and information on paper that would be wrapped around the bottle. Overall, packaging was basic, serving the primary purpose of protecting the medication from external contaminants.
However, as the medical industry advanced, so did the need for standardized and regulated packaging to ensure patient safety and facilitate the administration of medications.
Blister Packs and Pill Bottles
As medicine research advanced, so did the need for more sophisticated packaging. In the mid-20th century, blister packs, the ones we so often see today, emerged as a popular choice. This sealed, foil-based packaging, offered enhanced protection against moisture and air and helped in extending the shelf life of medications.
Glass bottles were becoming less common as plastic pill bottles became a more popular substitute. They provided a more user-friendly and portable alternative to the old, heavy, and fragile glass bottle.
The Rise of Regulation in UK Medicine Packaging
While advancements in UK medicine packaging were present throughout the 20th century, the greatest turning point came with the strict implementation of medicine regulations aimed at standardizing the industry. This was due to the fact that traditional UK medicine packaging and the lack of proper guidance and regulation were proving to be greatly limited in ensuring the safety of products and consumers.
Regulatory agencies have been present globally since the beginning of the 20th century, but in the UK, the Medicines and Healthcare products Regulatory Agency (MHRA) has been at the forefront of setting guidelines to ensure the quality, safety, and efficacy of medical products since 2003.
Their main responsibilities include:
Since its implementation, the United Kingdom has played a pivotal role in shaping the evolution of UK medicine packaging through its stringent regulatory framework. The MHRA consistently sets forth updated guidelines that govern the packaging of medicine, ensuring safety, efficacy, and adherence to quality standards.
Labeling Requirements of UK Medicine Packaging
UK medicine packaging is made up of many different components that are all strictly regulated and controlled to ensure its accuracy and safety for use and consumption.
One of the most critical aspects of UK medicine packaging is the labeling, or the information provided on labels. Regulations mandate that packaging must include essential details such as the name of the medicine, dosage instructions, expiry date, batch number, and manufacturer information, to name a few.
Additionally, UK medicine packaging labels often feature critical safety information, such as potential side effects and storage guidelines. The main goal of a label is to ensure that individuals administering or consuming the medication are well-informed about its proper use and potential risks.
Compliance with labeling regulations not only supports the safe and effective use of medicines but also plays a pivotal role in promoting transparency and accountability within the medical industry. Strict adherence to labeling requirements contributes to the overall goal of ensuring public health by providing users with all the necessary information and knowledge needed to make informed decisions about their healthcare.
Tamper-Evident Measures
Tamper-evident packaging is described as “having one or more indicators or barriers to entry which, if breached or missing, can reasonably be expected to provide visible evidence to consumers that tampering has occurred.”
These measures in UK medicine packaging play a crucial role in ensuring the safety and integrity of medical products. The measures are implemented to provide visible signs of interference, making it evident if a package has been tampered with or compromised.
Common tamper-evident features include seals or bands that are broken or altered when the packaging has been opened. By incorporating these features and measures, UK medicine packaging manufacturers aim to protect consumers from potential tampering, contamination, or unauthorized access to medications.
Tamper-evident packaging not only serves as an added layer of protection and security but it also builds trust among patients and healthcare professionals, assuring them of the authenticity and safety of the medicine inside a package. This added security measure contributes significantly to maintaining the quality and reliability of medicine products throughout the supply chain, ultimately safeguarding public health.
Child-Resistant Packaging
Another important addition to UK medicine packaging regulations came in the later half of the 20th century. Child-resistant packaging became a requirement, addressing concerns about accidental ingestions and poisoning of young children. This type of packaging is designed to be difficult for children under the age of five to open, thus reducing the likelihood of unintentional ingestion.
Child-resistant UK medicine packaging was first introduced into the United Kingdom in the mid 1970s but only became standardized in 2001. Since then, a number of different regulations have been put in place, including European and International standards, as well as the Human Medicines Regulations 2012 and GHS/CLP, which became fully effective in 2015.
Since its introduction, child-resistant packaging has undergone many changes, not only in increasing resistance to potentially being opened by children but also in optimizing usability for adults. There have been continuous efforts to increase the safety of these products and their packaging with constant new developments in packaging improvements.
Barcoding and Serialization
Barcoding and serialization are integral components of modern UK medicine packaging, designed to enhance traceability, authenticity, and overall supply chain security.
Barcoding involves the assignment of unique identifiers, typically in the form of barcodes, to individual medicine packages. This unique identification enables efficient inventory management, reduces errors in product distribution, and facilitates rapid tracking throughout the supply chain.
Serialization takes this a step further by assigning a distinct serial number to each medicine unit, allowing for precise tracing of products from manufacturing to distribution to the end-user. These measures not only contribute to streamlined logistics but also play a pivotal role in combating counterfeit medicine and in ensuring patient safety.
GMP (Good Manufacturing Practices)
Good Manufacturing Practices (GMP) in UK medicine packaging represent a set of strict quality standards and guidelines that medicine manufacturers must adhere to in the production of packaging materials and systems.
GMP regulations ensure that the entire product lifecycle, from development and production to labeling and storage, follows specific protocols aimed at consistently delivering safe and high-quality UK medicine packaging.
Compliance with GMP standards is crucial for maintaining the integrity of medicines and preventing contamination or defects in the packaging. These practices encompass various aspects, including personnel training, hygiene, documentation, and equipment calibration.
By adhering to GMP in UK medicine packaging, manufacturers uphold the highest standards of quality assurance, contributing to the safety and efficacy of medical products and reinforcing the trust of healthcare professionals and consumers in the integrity of the overall medicine supply chain.
Environmental Sustainability
In recent years, there has been a growing emphasis on environmental sustainability in UK medicine packaging. Regulatory agencies are encouraging medical companies to adopt eco-friendly packaging solutions, reducing the environmental impact of the industry.
Manufacturers increasingly focus on adopting eco-friendly practices and materials to minimize their carbon footprint. This includes exploring recyclable, biodegradable, or compostable packaging options and optimizing packaging designs to reduce material usage.
Additionally, efforts are being made to enhance energy efficiency in the production processes and choose environmentally responsible printing inks and coatings. The aim is to strike a balance between ensuring the safety and efficacy of medical products while minimizing the environmental impact associated with their packaging.
By embracing sustainable practices, the medical industry not only aligns itself with global environmental goals but also responds to the growing demand from environmentally conscious consumers.
Smart Packaging and Technological Integration
UK medicine packaging in the 21st century vastly differs from the packaging used over a hundred years ago. In recent years, technological advancements have revolutionized UK medicine packaging, with smart packaging becoming the newest trend in the industry.
Smart packaging refers to the emerging technologies within the packaging industry that increase consumer and business utility alike, all while simultaneously increasing the simplicity of accessing and tracking the information surrounding products and companies.
This packaging is equipped with features like temperature monitoring, NFC (Near Field Communication) tags, QR codes, and interactive labels. These innovations not only ensure the integrity of the medication but also empower patients with information and enhance overall healthcare management.
Innovation in UK Medicine Packaging – Automated Proofreading
As the accuracy of all packaging content is of extreme importance, technological solutions that ensure packaging integrity are also increasing in popularity. Automated proofreading is one of those innovative solutions in UK medicine packaging.
Automated proofreading aids in maintaining packaging accuracy by inspecting all types of regulatory content that would be present on UK medicine packaging. It helps companies uphold packaging and manufacturing standards with greater ease and efficiency, ensuring compliance with UK medicine standards and beyond. This technological innovation provides better proofreading results and enables higher-quality UK medicine packaging as it acts as an added layer of security in quality assurance processes.
In essence, automated proofreading works by comparing two documents to find discrepancies between the two. The innovative software conducts comprehensive inspections and proofreads all packaging assets from text, color, graphics, barcodes, braille, and more.
Through automated proofreading, inspections of packaging components are completed exponentially faster than traditional proofreading, and a task that once took hours or days to complete is now reduced to only a few minutes.
Benefits of Automated Proofreading
Automated proofreading plays a crucial role in enhancing the quality and compliance of UK medicine packaging. Some ways in which automated proofreading helps in UK medicine packaging includes:
By leveraging automated proofreading in medicine packaging, companies in the industry can improve the overall accuracy, quality, and compliance of their packaging. This not only increases patient safety but also helps maintain the integrity of medical products.
Customer Case Study: Automated Proofreading For Error-Free Medicine Packaging
Prior to implementing GlobalVision, all materials at Bristol-Myers Squibb (BMS) Shanghai were manually reviewed by their Quality Control department. Manually proofreading each packaging component often took too long and was too reliant on the SASS Project Manager. As they only relied on the human eye to catch errors, the risk of faulty inspections was high.
For a major pharmaceutical company such as BMS, letting a critical packaging error slip by could have damaging effects on its reputation. It may also result in reprints or recalls which can impose huge costs on the business. Worse, it can cause potential consumer harm if these packaging errors made it to market.
The BMS Quality Control Department uses GlobalVision to inspect incoming packaging materials such as cartons. Batch by batch, the packaging is compared to the approved samples to catch any differences between the two. As a result of the automation, the Quality Control Department has found that its revisions could be completed faster and more effectively.
Through the implementation of GlobalVision, BMS Shanghai increased its level of efficiency and accuracy, further aligning its commitment to quality when it comes to both packaging and patients.
The Future of UK Medicine Packaging
The transformation of UK medicine packaging throughout the years has been shaped by dynamic factors such as evolving regulations, changing consumer needs, technological advancements, and a heightened emphasis on safety and responsibility.
The industry, from basic glass bottles to cutting-edge smart packaging, has consistently adapted to meet contemporary demands, with the MHRA playing a pivotal role in maintaining and enhancing these standards.
Each advancement in the industry shows a commitment to ensuring the highest quality and safety standards. Notably, the integration of technological solutions, including automated proofreading tools, emphasizes this commitment by improving accuracy and safeguarding packaging and, by default, healthcare professionals and consumers alike.
Automated proofreading serves as a comprehensive solution that not only streamlines quality assurance processes but also facilitates accuracy and compliance for UK medicine packaging manufacturers and beyond.
To experience the transformative power of automated proofreading, request a demo of our innovative software and witness firsthand how this technology can revolutionize your daily business practices.
Revolutionizing Braille Inspection: Introducing the Upgraded GVD Braille Module
Date: December, 2023 | Category: Compliance | Author: Hana Trokic
In regulated industries, where adherence to standards and accessibility is crucial, Braille is a vital component of any product’s packaging or labeling to foster compliance and inclusivity.
Braille, a universally accepted system of writing designed for individuals with visual impairments, is critical in ensuring that information, particularly in industries subject to strict regulations such as pharmaceuticals, is universally accessible.
This code not only empowers individuals with visual disabilities by providing them with independent access to written content, but it also aligns with non-discrimination principles mandated by regulatory agencies.
From a quality control perspective, Braille Inspection and accuracy play an important role as Braille is mandatory on pharmaceutical packaging all across Europe, and is strongly recommended by the FDA in Western markets, while other regions such as the ASEAN markets are working to heighten inclusivity by implementing braille requirements on packaging soon.
For regulatory industries to ensure the complete accuracy of their products, they need to ensure comprehensive revisions and inspections of their content. This includes text, graphics, barcodes, colors, and of course, braille for an all-encompassing quality control process. One way to ensure this accuracy is through modern-day technological solutions and innovations that ease these critical yet demanding revision tasks.
The New GVD Braille Module
One such innovation that stands out for compliance reviews is the newest upgrade from GlobalVision—the GVD Braille Module. This new braille inspection technology sets a new standard for fast, accurate, and comprehensive braille inspections.
The GVD Braille Module allows regulated industries such as pharmaceuticals and print and packaging to automate braille height inspections with unparalleled granularity and speed, providing braille compliance data for each individual braille dot. This market-disrupting product brings unprecedented braille height detail, as well as meticulous braille translations to ensure complete accuracy and compliance with industry regulations across all printed assets.
This advanced technology is not just an upgrade in compliance inspections, it’s a breakthrough in braille inspection.
Here’s what to look forward to with the newest GVD Braille Module:
Unmatched Braille Inspection Speed and Precision
With 10X faster braille height inspections and the support of full-size press sheets, GlobalVision’s newest automation technology surpasses the traditional DotScan software and all other competitors on the market. Printing & packaging and pharmaceutical companies can now expect to automate braille inspections with granularity and speed that was previously not possible.
The technology not only accelerates the inspection process but also ensures unparalleled precision, reducing the risk of oversights. Beyond heightened efficiency, the increased automation of the entire compliance inspection process allows organizations to redirect resources to more strategic tasks, fostering innovation and growth internally.
GlobalVision’s braille inspection technology redefines industry standards by combining speed and granularity, transforming compliance inspections into a faster, more comprehensive and accurate process.
Save Resources and Eliminate Unnecessary Overhead
With this new release, all braille inspection features are embedded within the robust GVD platform. This allows companies in regulatory industries to save money and resources by eliminating the need and overhead of managing multiple systems.
The GVD Braille Module consolidates all packaging quality control processes as it is fully embedded within the robust GVD system, allowing for text, graphics, barcode inspections and more, rendering the use of a separate system obsolete.
This upgrade ensures that every aspect of your quality control process can be seamlessly executed within a single platform. The efficiency gains are unmatched, as companies can now navigate the entire process, including the previously tedious braille inspection, with speed and precision, while simplifying their workflows and enhancing overall productivity.
This innovation not only streamlines operations but also positions the GVD Braille Module as an industry leader, offering unparalleled ease and efficiency to the market.
Ensure Adherence to Compliance Regulations
For regulated companies, the need to adhere to strict guidelines and requirements is critical. GlobalVision’s latest advancement in braille inspection technology represents a crucial upgrade in addressing this concern by guaranteeing ongoing braille compliance with the Marburg Medium Font Standard as well as the ISO 17351:2013 requirements for braille labeling on medicinal products.
This upgrade not only ensures precision and accuracy in braille, but, more importantly, serves as a proactive measure to prevent potential regulatory sanctions. By aligning seamlessly with established standards, this technology provides regulatory companies with the assurance that their braille labeling processes are not only efficient but also in strict accordance with mandated guidelines, protecting against potential legal and regulatory penalties.
Global Scalability
The GVD Braille Module isn’t confined to a specific language or region. It scales globally, inspecting braille translations in an impressive 44 languages against a master file. This global scalability ensures that the technology is not only cutting-edge but also inclusive and diverse, catering to the many linguistic needs of multinational enterprises.
By accommodating such a wide linguistic range, the GVD Braille Module becomes a versatile tool that addresses the diverse needs of companies worldwide, acting as a positive lever toward their global expansion strategies.
Detailed Reports and Compliance Data
One of the standout features of the GVD Braille Module is its ability to provide you with highly detailed reports for each braille dot across all regions, ensuring that every single dot meets regulatory standards.
The GVD Braille Module allows you to achieve unprecedented granularity in braille inspections with in-depth reporting for each individual braille dot across all braille regions, including multi-panel regions. This means the software goes beyond basic inspection data and provides a level of inspection scrutiny unparalleled in today’s market.
The Future of Braille Inspection
In an era where technology and automation is the driving force behind progress, the GVD Braille Module stands out as a revolutionary solution in the field of braille inspection. This comprehensive solution surpasses all previous inspection systems and doesn’t just meet industry standards but sets a new benchmark for efficiency and accuracy.
As industries strive for greater innovation in technological solutions, the GVD Braille Module allows you to overcome all previous inspection limitations and embrace new technology that improves the entire quality control process.
GVD Braille Module is not just an upgrade, it’s a revolution in braille inspection. To try the new standard in braille inspection yourself, book a personalized braille demo and begin revolutionizing your compliance inspections today.
Manual vs. Automated Proofreading: A Comprehensive Guide
Date: December, 2023 | Category: Proofreading | Author: Hana Trokic
The way we communicate with others is essential. How we express ourselves through different outlets is crucial in getting our exact message across exactly how we intend it to.
The same can be said for businesses, as companies spend immense amounts of time, money, and resources ensuring they communicate their brand seamlessly to every consumer. Yet, a brand’s image isn’t just a mission statement or a slogan. Behind each brand is a mountain of content and documentation – from packaging and labeling to legal, digital and printed content.
It begs the question. Manual or automated proofreading? Which method will better ensure brand integrity when products go out to market?
What is Manual Proofreading?
Manual proofreading refers to the process of carefully reviewing and checking documents or content by human experts to ensure accuracy, compliance, and adherence to established standards and regulations. This process involves meticulous examination of the content for errors, inconsistencies, or any deviations from the regulatory requirements.
The Risks of Manual Proofreading
Manual proofreading implies human proofreading of all documentation before it goes out to print.
With an endless stream of documentation that needs to be constantly reviewed, manual proofreading is not without its challenges. Not only is it time-consuming, but the chance of human error is high, while some mistakes can result in significant consequences for companies, be it financial, legal, or brand-wise.
Other companies face the challenge of having documents that simply cannot be manually proofread since errors in barcodes, fine print, and graphics are often far too difficult for the human eye to detect.
While manual proofreading will always play an essential role in many quality assurance processes, it is important to note its many risks if used as a primary method of proofreading.
Some of the risks associated with manual proofreading include:
What’s more, manual proofreading is not highly accurate when dealing with graphics, color deviations, barcodes, or braille. Unless the mistakes are evident, the human eye cannot detect minor discrepancies that otherwise compromise the integrity of the overall design, packaging, label, and so on.
To stay competitive in today’s market, companies simply cannot afford the setbacks of manual proofreading. This is why many modern-day businesses turn to automated technologies to help increase the speed, accuracy, and efficiency of their revision workflows.
Want to learn more about the risky business of manual proofreading? Read our blog post here.
Automated Quality Control as a Proofreading Solution
Automated quality control and proofreading stands out as a perfect proofreading solution for businesses who wish to reduce the risks and setbacks that come from manual proofreading.
This technological innovation provides better proofreading results and enables complete and comprehensive inspections of critical content and documentation.
In essence, automated quality control and proofreading works by comparing two documents to find discrepancies between the two. The software conducts comprehensive inspections and proofreads everything from text, color, graphics, barcodes, braille, and more. Inspections are completed exponentially faster than manual proofreadings and a task that used to take hours or days is now reduced to only a few minutes.
The Benefits of Automated Proofreading
Automated quality control and proofreading offers several advantages across various industries and processes.
Some key benefits include:
To learn more about how automation can help your organization avoid costly mistakes, read Manual Proofreading Errors: How to Stop Label Recalls in Your Supply Chain
Automated Proofreading for Error-Free Content
One area where companies can largely benefit from automated quality control and proofreading is packaging and labeling. Pristine, error-free packaging and labeling not only increases customer loyalty to your brand, it’s also a necessity, regardless of industry.
It ensures that companies meet strict regulations from regulatory agencies such as the FDA for the United States, the MHRA for the United Kingdom, and EFSA for the European Union to name a few. This helps avoid potential compliance issues that lead to severe consequences.
Error-Free Packaging and Labeling
A packaging or label error doesn’t have to be fraudulent to be costly. In fact, a great deal of mistakes are simply caused by human error. Market research indicates that 60% of product recalls are caused by human oversights.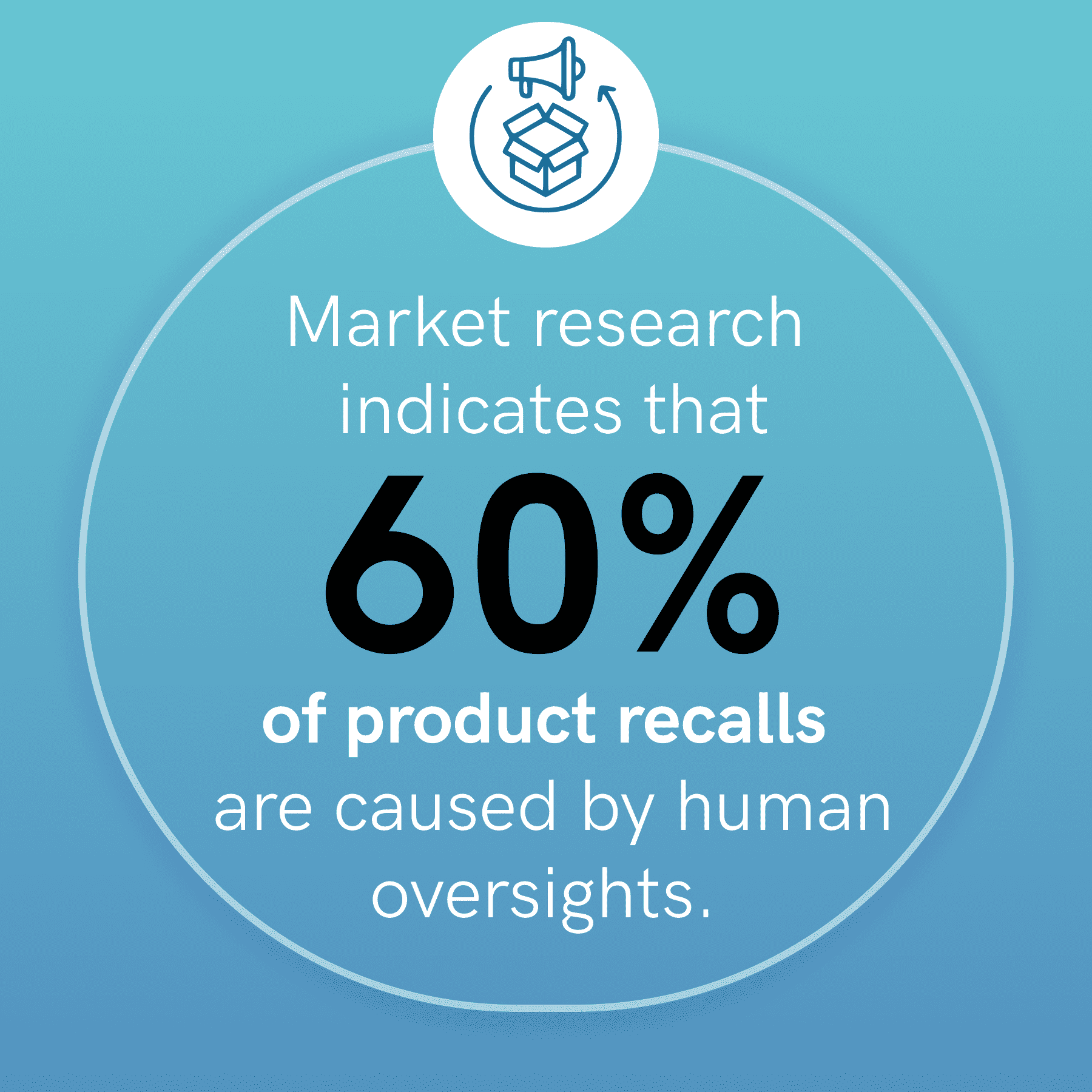
Human errors can easily be introduced and missed in content and only reinforce the need for added layers of reassurance, such as automated quality control and proofreading software.
Performing label and packaging inspections at each stage of the revision cycle reduces the risk of a recall and the number of required revision cycles, so products get to market faster, without any errors.
Consequences of Label Errors
Taking the food and beverage industry as an example, packaging must contain what the label entails. If the FDA has reason to believe packaging is inaccurate, that it falsely claims the contents of the product inside, imports can be detained without physical examination. The product effectively gets prevented from being distributed and ultimately sold.
If a manufacturer is found to be guilty of breaching FDA regulations and compliance, the FDA may issue a warning. In the event the manufacturer does not comply and correct the issue, the FDA takes additional legal action to ensure the product gets removed from the market, without it being permitted to return until the issue has been corrected. Criminal fines and even prosecution may result depending on the infraction.
In the case of the pharmaceutical industry, which is also under the purview of the FDA and whose customers depend on packaging for accurate dosage information, it’s easy to see why penalties need to be especially severe. A single misplaced period can have huge negative ramifications.
Find out more about creating error-free content by reading Why Error-Free Packaging and Labeling Is a Must
Tips for Creating Error-Free Content
There are many different components involved when creating content for regulated industries, which includes packaging and labeling. To help ensure that you create error-free content and reduce the risk of dealing with a product recall, it’s always helpful to implement some best practices.
Proofreading Starts With Up-to-Date PDFs
Throughout a proofreading cycle, a PDF can go through many revisions before getting approved. Files can also be stored across different network shares or even on an individual’s local computer. It’s key to ensure you know where to find the most up-to-date PDF. By doing so, businesses will avoid sending the wrong PDF to print.
Check Barcodes Early
It’s common for graphic artists to put placeholders for barcodes to show where the final barcodes will be positioned on a file. An FPO symbol will often be placed on top of a barcode which stands for “For Position Only.” This is often missed when the print runs, resulting in the correct barcode not appearing.
It’s recommended to check barcodes on proofs which can be done through automated quality control and proofreading for checking barcodes or printing out the proofs and using a handheld verifier.
Proofread Printer Proof Prior to Approval
It’s easy enough to give a quick glance over artwork files and tell the printer to go ahead with the job, but this is not enough to ensure no mistakes have slipped through.
Conducting a thorough proofreading of files to check for errors in spelling, color, barcodes, and other content on a proof is essential. One way to do this type of check is to do a line-by-line visual comparison.
Standardize Design Tools
Do you know what versions of Adobe Illustrator your suppliers are using? Chances are they are all using different versions, which equals different functionalities and feature sets.
Ensuring everyone is on the same version means everyone is viewing the same file and that you have repeatable results. This also ensures there won’t be any unintended changes due to differences in software.
Continuous Quality and Improvement
Continuous testing in software is the new approach when developing products. Most software products today will have some level of automated testing completed to check against expected results. This helps to continuously test code and ensure quality throughout the development process.
Read 6 Tips for Creating Error-Free Packaging for more information about how to create perfect content every time.
There’s no reason why this methodology can’t be applied to any business’s revision cycle, regardless of industry. Using tools to perform routine tasks like preflight and PDF comparison can enable automation on a continuous basis to catch errors in files early on before products go out to market.
By implementing these best practices, businesses will see an immediate reduction in errors and an overall improvement in quality.
Want to learn more about automated quality control. Read our guide An Introduction to Automated Quality Control
Automate Your Manual Processes
To keep up with modern trends and ever-growing consumer demands, manual proofreading is simply not an adequate solution to allow for proper functions within a company’s quality assurance workflow.
While traditionally manual proofreading was the only method used to revise critical documentation, modern-day technology and innovations have allowed for more intelligent, more efficient solutions to get the job done.
With endless benefits and countless advantages to your workflow, automated quality control and proofreading is the leading solution for companies who want to revolutionize their revision processes.
To ensure the complete integrity and accuracy of all files, request a demo of GlobalVision today, and learn about all the advantages it can bring to your company while modernizing your current practices.
———————————————————————————————————————————————————
Related Articles:
Dempsey Corporation Transforms the Label Review Process with GlobalVision
Date: November, 2023 | Category: Customers | Author: Hana Trokic
About Dempsey Corporation
With over 35 years of experience in the consumer goods industry, the Beauty Division of Dempsey Corporation understands the complex needs of customers when it comes to product development, sourcing, quality assurance, and logistics.
Located in Toronto, Ontario, Dempsey’s Beauty Division is a private label that produces an array of products under common retail brand names. With a commitment to going above and beyond for their customers, Dempsey recognizes the importance of a strong quality control process.
Today, Dempsey is represented by a diverse group of international experts based in five countries with the one main goal of delivering value.
The Challenge: Ensuring Accuracy of Large, Complex Files
Prior to implementing digital quality control, the company was outsourcing specific elements of the label review process. Numerous label versions were created with label workflows interchanging between internal teams, clients, and packaging producers.
For Dempsey Beauty’s quality assurance team, this led to difficulties in managing approvals, especially with regard to ensuring that all teams were using the most recent and relevant version of a file.
What’s more, with product labels containing large ingredient lists which are very text-heavy, manual proofreading became increasingly difficult, especially when the team started succumbing to proofreading fatigue, occasionally missing some content errors as their eyes started to adapt to the content. Ultimately, these errors often resulted in financial losses as well as reputational damage.
Before implementing GlobalVision, the majority of proofreading fell into the hands of one person to review labels at the regulatory and quality assurance levels. This created a vulnerable and risk-prone step in their process, as the onus fell on the proofreader – a single person who mainly relied on the human eye for quality control.
To help reduce the risk of human error and assure the accuracy of their large volume of labels and content, Dempsey decided a change was needed in their quality control process to ensure the credibility and accuracy of their products, and maintain their position as a leader and household name in the beauty industry.
The Solution: Replace Error-Prone Label Review Processes with Accurate Automated Solutions
After exploring various solutions on the market, Dempsey Corporation made the decision to incorporate GlobalVision into their quality control processes to eliminate errors and fatigue caused by manual proofreading.
They decided to implement this automated solution as an additional layer of review, giving them peace of mind and allowing them to focus more efforts on other important areas of quality assurance.
Additionally, Dempsey’s Beauty Division wanted to improve their market position and stand out against competitors, and they felt that implementing GlobalVision would contribute to their success in this area. “It’s the gold standard of quality assurance, to be able to assess a label with the same level of scrutiny regardless of the number of labels there are and how tired your eyes might be,” says Charles Inthathirath, the Quality Assurance Manager at Dempsey’s Beauty Division.
The Result: Increased Productivity With GlobalVision’s Automated Software
After implementing GlobalVision’s Quality Inspection Platform, the company has benefited from significant time-savings along the entire quality control process. In high season, Dempsey’s quality department can use the GlobalVision software to replace half a day’s worth of label reviews, allowing them to review more labels in a shorter time period.
When it comes to replenishing inventory in the production phase, having GlobalVision has been a huge help in approving labels that are in queue for print.
Aside from accelerating text-heavy reviews, the quality team appreciates GlobalVision’s barcode inspection tool, especially the human-readable value and grade provided by the software, which allows them to ensure that barcodes are always compliant with industry regulations before they go to print. . “Overall, the software is great! We also appreciate the extra training available to us,” says Inthathirath.
They’ve been able to measure the success of implementing GlobalVision by measuring their productivity levels. With GlobalVision in place to help improve the efficiency of their label review process, the quality department has been able to allocate resources to other areas of quality assurance and they’ve seen an increase in efficiency across the board.
Looking Ahead with GlobalVision
As they look towards the future, the company sees itself moving forward by expanding their beauty line to include eye products while also pushing towards more environmentally friendly and sustainable packaging.
Going above and beyond to meet and exceed the needs of their customers will always be top priority for Dempsey’s Beauty Division. That is why they continue to use GlobalVision in their label reviews to ensure the complete accuracy, credibility and quality of every product that goes out to the market.
A Beginner’s Guide to Sustainable Packaging
Date: November, 2023 | Category: Quality | Author: Hana Trokic
While “going green” may be a proud point for many businesses in this day and age, in the world of packaging and design, it’s not necessarily going far enough. Instead, it’s all about being sustainable.
However, true sustainability doesn’t just take into account the materials that go into packaging. True sustainability also considers potential waste during the production process. When introducing end-to-end sustainability, businesses need to look back to the very beginning, to the point where the packaging is designed and then approved.
It is important to note that the packaging approval process can result in many rounds of revisions until everything is ready for production. The result can create wasted resources if your process isn’t as tight as possible, even if the packaging itself is 100% sustainable.
As a result, significant resources get wasted when mistakes slip through your supply-chain cracks. Avoidable errors can result in recalls leading to heaps of wasted packaging that have no value. For perspective, in 2015 alone, 77.9 million tons of municipal solid waste generated in the United States consisted of containers and packaging. Over one-third of that total ended up in landfills.
Read on to discover how to create truly sustainable packaging and processes for your business.
What Is Sustainable Packaging?
While a product that’s labeled as “green” carries a positive, eco-friendly connotation, it’s vague by standards set by the Federal Trade Commission.
For example, “green” generally means one or some combination of the following:
“Green” may sound satisfactory, but each of the above actually conveys something tangible. According to Diana Fryc, Director of Operation of Retail Voodoo, using compostable packaging is just one step.
“Aside from compostable packaging, there is still a strong desire to reduce the size of packages, continued desire to use fewer adhesives, and continued use of the post-consumer recycled material,” she says. “Lighter materials to save on shipping costs and form factors that maximize shelf space bottles will also continue.”
In fact, packaging that’s “sustainable” is understood to meet a long list of specific criteria, featuring many of those same characteristics. To further illustrate this point, the Sustainable Packaging Coalition has developed its own criteria for what defines sustainable packaging:
Of course, the International Organization for Standardization (ISO), the Consumer Goods Forum, and CEN all have alternative packaging standards. So, globally speaking, there aren’t any hard, fast rules for what constitutes sustainable packaging. There are, however, certain guidelines.
Following them is far from easy, but this guide will help you understand the basics as you maneuver through the complex world of sustainable packaging and its implementation.
Reducing Your Carbon Footprint
Ultimately, by introducing sustainable packaging into your supply chain, businesses are aiming to reduce their carbon footprint as a whole. This includes securing product packaging workflow through effective quality control.
Preventing recalls by catching errors means less packaging, less waste, and therefore, a lot less energy consumed. After all, the resources needed to carry out recalls, which cost on average $10 million in the food industry, don’t include the transportation and labor costs of putting more packaging through your supply chain and re-shipping the product. It all affects your bottom line and the packaging footprint you’re trying to market as sustainable.
Therefore, it’s time to start looking beyond the product and at the complete end-to-end process. Many companies are integrating new technologies and automated systems that can spot errors before going to print as a pre-emptive strike against recalls. The main goal is to address sustainability, as it’s important to consider how products are made and how to be as efficient as possible with the resources available.
It turns out the idea that integrating sustainable packaging leads to higher costs is actually a myth. Studies show that companies that look to become more eco-friendly overall enjoy as much as an 18% return on investment increase. That’s potentially a lot of green for going green.
Have you heard about footprint packaging? Learn more by reading our detailed blog post.
The Need for Sustainable Packaging
There’s little denying the benefits of sustainable packaging. There are financial benefits in store for any corporation moving in that direction. That’s not just due to the increased back-end efficiency and economies of scale that result from such a move.
If marketed correctly, sustainably packaged products have been proven likely to sell more.
Obviously, a company shouldn’t make the switch simply to appease its conscience. All things being equal, it just makes sense to waste less and promote a brighter future filled with less waste.
“Packaging is a polluting factor” says Andreas Kioroglou, the CEO of Matador Design. “Creative design will [start to] take into account factors like the reduction of the carbon footprint of packaged goods throughout the supply chain and designs that will extend the packaging life cycle.”
Read what more experts are saying about sustainable packaging here.
Over the long term, it is expected that sustainable packaging solutions will lead to higher profits relative to one’s current process. The only thing holding companies back is the inevitable, albeit short, discomfort that results from transitioning to a new and improved process.
Implementing Sustainable Packaging
Packaging plays a crucial role in influencing customers’ buying behavior, yet unsustainable packaging can damage the reputation of a company, causing customers to switch to other brands that employ environment-friendly materials and processes.
Unsustainable packaging is detrimental to the environment as it increases the amount of waste that is diverted to landfills, causing increased greenhouse gas emissions.
Sustainable packaging can reduce our ecological footprint at all stages of the product life-cycle, helping the manufacturer and the customer work towards a sustainable future.
With sustainability being the major agenda for almost all countries around the globe, several organizations are introducing sustainable packaging in order to reduce the negative impact on the environment and differentiate themselves from the competition.
However, the industry is not devoid of misconceptions that could cause confusion, making it challenging for organizations to work toward a sustainable future.
Sustainable Packaging Is An Added Cost
It is a common belief that a majority of product improvements come with a high price tag. Though the cost of sustainable packaging may seem to be high initially, it offers numerous benefits that contribute to the long-term success of a business. Moreover, socially responsible businesses incorporate the extra cost of sustainable packaging as a part of their business plan, assuring them of profits in the long term.
Adopting sustainable or green packaging enables marketers to connect with their eco-conscious and green-aware consumers, giving them a competitive advantage and boosting profits. In fact, studies conducted by the Carbon Disclosure Project (CDP) prove that organizations that adopt eco-friendly materials and processes are likely to see a return on investment of 18 percent or more.
Apart from attracting new customers and boosting your corporate image as an environmentally-responsible organization, sustainable packaging also offers innovative designs that can be tailored to the clients’ specific requirements.
For instance, waste can be recycled using the paper molding process and converted into customized packaging in order to meet the firm’s requirements for heavy and delicate products at an extremely affordable rate. All this eliminates excessive packaging, making the shipments light and drastically reducing the products’ footprints on the store shelves.
Additionally, in recent times, brands cannot afford to ignore eco-friendly strategies. Consumers increasingly prefer products that protect the environment, reduce global warming, and prevent air and water pollution.
Consequently, both emerging and advanced markets are drifting towards ethical and environment-friendly options, pushing designers, marketers, and package development experts to meet the right social and environmental standards.
Most countries also offer special subsidies and incentives for businesses that are looking to join the sustainability bandwagon. Moreover, firms going the sustainable way also enjoy preferential terms and tax rebates from the state and local authorities for setting up an environment-friendly business.
Thus, green packaging actually stands to save money by reducing material and shipping costs and minimizing waste, playing a persuasive role in helping customers choose your brand over the competition.
Sustainable Packaging Choices are Limited
With the growing concern regarding waste being diverted to landfills and the ensuing greenhouse emissions, customers are expecting firms to use eco-friendly elements in their products.
Consequently, packaging firms have come up with several innovative and green materials, namely polylactic acid (PLA), bagasse, recycled paper, and post-consumer polystyrene that can be used to manufacture coffee cups, plates, cutlery, and boxes.
For instance, Evocative, a New York-based biomaterials firm developed a mushroom-based material that can be used as an alternative to plastic packaging. Similarly, Biopac, a UK-based bioplastic developer uses polylactic acid (PLA) from renewable plant sources to manufacture compostable cups and food packaging.
Sustainable Packaging Adds to Waste
Sustainable packaging is not merely about the eco-friendly nature of the final product. Instead, it means that the packaging material is made from biodegradable, reusable, and environmentally-safe matter and uses energy-efficient manufacturing procedures and health-friendly working conditions for the staff involved.
Sustainable packaging helps firms streamline the packaging design, eliminating unnecessary material from the processes and creating less packaging-related waste. Materials such as biodegradable plastics, plant-based plastics, and recycled products are used to develop sustainable packaging, making it possible for manufacturers and consumers to reduce the amount of waste being diverted to landfills and the ocean floor.
For instance, molded fiber products, namely egg trays, fruit-and-vegetable trays, compostable plant holders, and wine shippers are made using biodegradable waste procured from recycling companies and individual households.
Sustainable Packaging is Unappealing to Consumers
Most commonly, when people think of sustainable packaging they envisage a dull brown or cream paper with visible reused fibers. However, technology has made it possible for design firms to come up with innovative packaging that harnesses powerful aesthetics and is environment-friendly at the same time.
Many international brands and powerhouses such as Samsung, Zara, and Puma offer attractive packaging yet use 100 percent eco-friendly material, preserving the planet and its natural resources.
Want to learn more about sustainable packaging myths? Click here to read our in-depth blog post.
Transitioning to Sustainable Packaging
While some companies are already fully onboard the sustainable packaging bandwagon, others are either on route to making the transition or have yet to make a firm decision on the matter.
For the companies already in existence, it’s about altering the course. Once you’ve committed to making the leap, it’s important to determine your ultimate goals. While the Sustainable Packaging Coalition’s criteria favor a circular economy (or closed loop, which relies on renewable energy), it’s by no means the only choice.
Another is to develop packaging with a linear lifecycle. There, packaging ultimately ends up as trash instead of biologically degrading. It can also be considered eco-efficient, depending on other production factors. It also means bigger short-term gains. The closed loop means more risk and long-term investment, but a higher potential payoff through legitimately sustainable packaging.
Here are some tips to help execute a proper sustainability strategy:
Automation to Sustainability
Automated quality control tools are indispensable assets for businesses striving to enhance their sustainable packaging processes. These tools, driven by cutting-edge technology offer multifaceted advantages that extend far beyond mere error correction.
In the context of sustainable packaging, precision is paramount. This software meticulously scans through all packaging-related content, including labels, product descriptions, usage instructions, and promotional materials, ensuring that they are free from spelling, grammar, and formatting errors. By maintaining a high standard of accuracy, businesses reduce the likelihood of recalls, reprints, and costly product corrections, directly contributing to a more efficient and eco-friendly production process.
By preventing errors, reducing rework, and promoting sustainability, automated proofreading software helps minimize waste in the production process and optimize resource utilization. They aid in curbing the overuse of materials and energy while contributing to the reduction of the carbon footprint associated with packaging.
In the eyes of environmentally-conscious consumers, these efforts resonate as a genuine commitment to sustainability, ultimately enhancing a company’s brand reputation and its competitiveness in the market.
Automated quality control is not just about catching typos; it’s a vital enabler in a business’s journey toward sustainable packaging. The software streamlines operations, reduces costs, encourages green thinking, and helps businesses establish themselves as responsible actors in environmental protection and sustainability.
As sustainable packaging gains increasing importance in today’s eco-conscious world, this technological solution is becoming an indispensable instrument for companies committed to both excellence and environmental consciousness.
A Sustainable Future
The global packaging and protective packaging market was valued at $1.0 trillion in 2021, and is projected to reach $1.5 trillion by 2031, which would result from steady year-over-year growth.
Innovation will logically end up being one driver of that valuation, just as it is currently in the manufactured goods sectors directly reliant on it. That’s simply the nature of a free-market economy in which consumers reward the cutting-edge.
As a result, it’s no longer a matter of going green. It’s arguably not even about going sustainable. It’s about striving to reach sustainability. As the exact definition of “sustainable” is a fast and moving target, it’s more a matter of taking steps towards attaining that goal.
In a period of just three years, the number of firms listed on the S&P 500 that included sustainability issues in their Securities and Exchange Commission filings increased from 5% to 25%. That in and of itself may not be a testament to how successful sustainability can be, but it is of how the times are becoming more eco-friendly.
Joining in on the success means changing with the times, or, perhaps more accurately, adapting. Both customers and the companies behind the products they consume stand to benefit from the large-scale evolution of packaging, which is taking place right before our eyes.
If you would like to take a step into implementing sustainable packaging into your business, start by implementing smart, technological solutions that can easily help you get there. Automated quality control is a comprehensive solution that will not only streamline your proofreading and quality assurance processes, it will also help your business achieve true sustainability with far greater ease.
Request a demo of our innovative proofreading software and see how this technology can revolutionize your every day, sustainable business practices.
How AI Proofreading Will Power the Future of Pharma
Date: November, 2023 | Category: Proofreading | Author: Gabriella Naguib
In the rapidly evolving pharmaceutical landscape, accuracy, compliance, and speed of regulatory processes are key. Traditional proofreading and compliance review methods for documentation and packaging, labels, and more have proven to be time-consuming and error-prone, often leading to delays to market, financial losses, non-compliance issues, and consumer safety risks.
The introduction and recent rise of artificial Intelligence (AI) and automation proofreading technology allow pharmaceutical companies to reap significant competitive advantages by streamlining workflows, reducing errors, and getting to market faster for often life-saving drugs. Consequently, these technologies also protect consumers and patients from potential adverse effects or improper use.
Pharmaceutical companies that are ahead of this technological curve are already benefiting from the introduction of AI and automation in their workflows. Heightened accuracy, compliance, and speed are only some of the advantages they reap, but as the technology continues to grow and develop, regulated industries–especially pharma–can expect to continue to benefit from such technologies in the future.
What is Artificial Intelligence (AI)?
AI focuses on creating intelligent systems capable of simulating human-like intelligence. Machine learning is one of the most popular techniques used in AI, which allows computers to learn from data, recognize patterns, and make decisions. These capabilities enable AI systems to adapt and enhance their performance over time.
The field of Regulatory Affairs within the Life Sciences industry is currently undergoing a significant transformation, thanks to the emergence of AI-powered technologies. These technologies are currently being utilized in Regulatory Technology (RegTech) to improve end-user performance. However, the potential for future use cases is vast. Although the use of AI in this field is currently relatively new, the RegTech industry is expected to grow from 7.08 billion in 2023 to 40.83 billion by 2030, and is well-positioned to leverage the power of AI.
How Pharma Regulatory Leverages AI Proofreading
A G2 study from June 2023 reveals that artificial intelligence and machine learning are the primary technologies used for compliance procedures, assisting in risk assessment, crisis management, and predictive analytics.
A prime example of how regulatory professionals in the industry leverage these technologies to automate compliance procedures is through AI-powered solutions. One emerging and innovative cloud-based proofreading software that is changing the way regulatory businesses are using automation in their quality assurance processes is, Verify.
Verify is the newest and most innovative proofreading software from GlobalVision that harnesses the power of AI to conduct accurate and thorough inspections of regulatory documentation. It allows regulatory users to perform quality checks across critical content such as digital packaging assets and labels by automating key tasks such as text inspection with character for character precision.
A key component of these quality checks is the ability to inspect documents whether they contain live text or not. To facilitate this, Verify has built-in OCR (Optical Character Recognition) capabilities that are driven by artificial intelligence. By leveraging these technologies, regulatory affairs professionals can handle reviews such as regulatory submissions and labeling inspections with complete ease, in record time.
The Advantage of AI Proofreading
GlobalVision’s independent market research has recently shown that AI-powered technologies help pharmaceutical companies get their products to market faster. Our survey results revealed that 89% of our regulatory survey respondents said that using our AI-powered automated proofreading solutions significantly reduced their compliance review process, allowing them to deliver products to market faster.
These findings provide strong support for the same claim through a customer case study involving a large pharmaceutical enterprise. The case study revealed that prior to implementing our AI-powered automated proofreading solution, the company had difficulties getting their products to market ahead of competitors, which ultimately hindered their ability to capture any market share in certain instances.
Elevating Core Technology with AI Proofreading
Beyond Optical Character Recognition (OCR), the industry is delving into a realm where AI plays a pivotal role throughout the entire content management and review process. In the near future, substantial improvements driven by machine learning will allow RegTech solutions to surpass the confines of rule-based systems that have previously governed SaaS proofreading algorithms.
This new ‘AI era’ presents an unprecedented opportunity. Tech companies can now “teach” their algorithms how to comprehend documents by continuously feeding them vast volumes of data over time. The result? Faster, better, more streamlined workflows and quality control processes that ultimately lead to more accurate inspections and content.
What’s more, as time passes, it is inevitable that these solutions will further improve and transform into “intelligent technology” at their core, designed with increasing precision to meet the unique needs of each and every customer.
AI to Simplify User Experience
With this strategic shift and AI at the forefront, regulatory users can expect even further automation for a multitude of tasks throughout the content management workflow, without compromising their trust in these technologies.
The automation of said tasks will be infused with a deeper, more human understanding of the documents that regulatory professionals review on a daily basis.
Imagine a level of understanding that encompasses simple nuances such as page numbers, document types (IFU, QRD, SPL templates, inserts, cartons), and structural components, including prescribing information highlights, tables of content, full prescribing information, forms, strengths, warning statements, dosages, and even the correctness of dosage units.
With this technology constantly expanding and becoming more common in regulatory workflows, users can look forward to a transformative end result that enhances their workflow and instills confidence in the technology they rely on daily.
What this means is as AI-driven proofreading technology advances, it promises faster and more accurate error detection. AI’s rapid analysis of large volumes of text will enhance productivity and ensure quicker turnaround times. The improving accuracy stems from machine learning algorithms that understand context, offering nuanced suggestions that will improve the overall quality of content.
Moreover, AI’s adaptability will allow for personalized proofreading, aligning with individual organizations needs and goals. This evolving technology can be used to not only detect text errors but beyond that, including graphics, formatting, color, braille, and barcode errors providing relevant insights catered to each specific business.
The final benefit to end-users is the seamless and highly efficient automation of numerous quality control tasks. In essence, AI-enhanced proofreading will transform and streamline the entire revision process, fostering comprehensive, efficient, high-quality content across various workflows.
AI Proofreading for Medical Terms
Going a step further, the first step into this journey could involve AI applications to detect and analyze medical terms by harnessing the power of machine learning. This new approach would revolutionize how medical dictionaries are managed and updated, making for a more sustainable and effortless approach for SaaS providers, as opposed to constantly cross-referencing to a medical dictionary such as Stedman’s Medical Dictionary.
Users would benefit by being able to rely on a continuously updated AI engine to detect and inspect medical terms and eliminate the risk of non-compliance issues occurring. It would also eliminate the need for tedious and time-consuming manual checks of medical terms that aren’t included in a specific dictionary.
AI Proofreading for Allergens
Much like medical terms, allergen statements is another area of exploration that this exciting new field presents. With the assistance of machine learning, solutions could flag allergen statements and analyze their components at the same level as a human reviewer. This simple addition promises to automate compliance reviews, eliminate laborious manual checks, and contribute to the elimination of recalls and non-compliance sanctions.
The applications of AI for medical terms and allergen statement reviews could potentially help users meet FDA requirements in those areas as well as the requirements of other global health authorities.
AI Proofreading in the Future
In conclusion, AI and machine learning hold vast potential for widespread adoption in regulated industries and the possibilities are endless.
While the level of trust in AI is still evolving, the role of artificial intelligence in proofreading will continue to grow steadily. And while human intelligence remains an indispensable asset in the revision and quality control process, for the foreseeable future in regulated industries, AI will act as a trusted assistant and an added layer of inspection when dealing with critical and regulatory documentation.
Want to learn more about how AI can help elevate your regulatory business? Download our Regulatory Insights Report: The Rise of Automation Technology in Regulatory Affairs and take a deeper dive into more compelling data from regulatory professionals and their use of technology.
If you would like to start experiencing the time-saving and compliance enhancing powers of AI and Verify, get started today with a Free Trial.
*****
Are you interested in being part of the future of our AI-powered technology? We are looking for Verify customers and prospects to participate in our beta group for new AI technologies – our Innovation Advisory Board. Have your voice heard and sign up here.
Compliance in Medicine Post Brexit: Everything You Need to Know
Date: November, 2023 | Category: Compliance | Author: Hana Trokic
As we continue to process the historic decision of the United Kingdom to exit the European Union, commonly known as Brexit, its far-reaching implications continue to unfold across various sectors. In terms of healthcare and pharmaceuticals, the repercussions are expected to be particularly noticeable and profound.
After years of negotiations and political turbulence, Brexit, which officially came into effect on January 31, 2020, has cast a shadow of uncertainty over the pharmaceutical industry in the UK and the EU.
The intricate web of Brexit’s impact on medicine compliance, pharmaceutical trade, and regulatory frameworks is yet to be fully understood but one thing is for certain – it’s multifaceted and intertwines issues of access to medicines, the integrity of pharmaceutical supply chains, and the development and approval of new drugs.
From supply chain disruptions stemming from customs and border checks to evolving drug approval processes as the UK establishes its own regulatory path, we look at how this shift is reshaping the landscape of medicine compliance and pharmaceuticals in the UK and EU.
By navigating the complexities and challenges faced by pharmaceutical companies, healthcare providers, and patients, read on to learn more about the strategies and adaptations emerging in the post-Brexit era to ensure the continued delivery of safe and effective medicines to those who rely on them.
Medicine Compliance in the UK Post Brexit
One of the immediate concerns that surfaced with Brexit was its impact on medicine compliance. Prior to Brexit, the European Medicines Agency (EMA) played a central role in regulating and approving medicines across the EU, including the UK. However, with the UK’s departure, the country’s Medicines and Healthcare Products Regulatory Agency (MHRA) became a stand-alone body as it ceased to be part of the European system of approval.
This transition led to a series of challenges, including the need for pharmaceutical companies to duplicate their efforts by submitting separate pharmaceutical applications to both the EMA and MHRA for approval.
This duplication not only increased regulatory burdens but also posed questions about the consistency of medicine approvals and what compliance is in medicine post Brexit.
Patients and healthcare providers needed assurance that the medicines they relied on remained safe and effective. Consequently, many pharmaceutical companies undertook the arduous task of adapting to these new compliance requirements, investing time and resources to ensure a seamless transition.
The Pharmaceutical Trade Landscape
The pharmaceutical industry relies heavily on global supply chains, making it particularly vulnerable to disruptions caused by Brexit. The imposition of customs and border checks created bottlenecks and delays, affecting the timely delivery of vital medicines to patients on both sides of the English Channel.
Pharmaceutical companies were forced to reevaluate their supply chain strategies, with some choosing to stockpile medicines to mitigate potential shortages. However, stockpiling is not a sustainable long-term solution and comes with its own set of challenges, including increased storage costs and the risk of medicines expiring before use.
Moreover, the UK’s departure from the EU single market and customs union introduced new regulatory barriers to pharmaceutical trade and new medicine compliance rules. Companies had to navigate complex rules of origin, tariffs, and customs procedures, all of which added to the cost and complexity of doing business.
To address these challenges, some pharmaceutical firms explored the possibility of relocating parts of their operations to the EU to maintain access to the single market. This then leads to the potential of further economic consequences for the UK as valuable companies and jobs are no longer located on English territory.
Parallel Importation
Another challenge that arose was the stricter regulations regarding parallel importation.
Parallel importation refers to the practice of importing pharmaceutical products from one country to another within the European Market Area (EMA) to take advantage of price disparities. After Brexit, the UK is no longer part of the EU single market, meaning parallel importation became significantly harder.
They are now subject to stricter medicine compliance regulations and have to apply for licenses to import goods that could have easily been shipped throughout the Euro Zone prior to Brexit. In the future, this could affect the availability of certain medicines and their cost in the UK.
Customs and Supply Chain Disruptions
While exiting the EU made certain things easier for the UK, it certainly also introduced many more regulations and complications with regard to trade between the two European territories.
Brexit introduced customs checks and border controls between the UK and the EU, which has been shown to lead to supply chain disruptions for pharmaceutical companies. Delays in transporting raw materials and finished products can, and to an extent, have impacted the availability of medicines on both sides of the border.
Pharmaceutical companies have had to adjust their supply chain strategies to mitigate these challenges, but the potential for even more disruptions remains a large concern.
The Evolution of Drug Approval Processes
Brexit also prompted a shift in the landscape of drug approval processes.
The UK now had the opportunity to develop its own medicine compliance regulatory framework, separate from the EMA. While this could potentially streamline decision-making and reduce bureaucracy, it raised concerns about the duplication of efforts and the potential for divergence in standards between the UK and the EU.
To mitigate these risks, the UK and EU agreed to a medicine compliance regulatory cooperation framework, ensuring continued information sharing and collaboration on drug approvals. However, challenges remain as the two entities adapt to their new roles and responsibilities in this post-Brexit era.
Pharmacovigilance and Safety Reporting
Pharmacovigilance, the monitoring of the safety of pharmaceutical products once they are on the market, is a crucial part of the pharmaceutical product lifecycle, and another area affected by Brexit.
The UK and the EU now have separate pharmacovigilance systems, leading to the need for separate safety reporting and data management processes. Ensuring seamless cooperation and information exchange between these systems is crucial to maintaining patient safety and medicine compliance.
Yet, with the additional regulations being placed after Brexit and the further complication of the entire process, the chance of errors occurring is higher, therefore, the need to mitigate them is also a larger concern.
Medicine Compliance Strategies and Adaptations
In the face of these medicine compliance challenges, pharmaceutical companies, healthcare providers, and patients have to quickly adapt to the post-Brexit reality.
Strategies to ensure the continued delivery of safe and effective medicines include:
Document Comparison Software: The Ultimate Post-Brexit Strategy
Along with the strategies mentioned above, document comparison software offers significant advantages in the domains of medicine compliance, pharmaceutical trade, and post-Brexit regulatory adherence.
It aids medical facilities in maintaining – medicine compliance by ensuring the accuracy of regulatory content, supporting version control, and facilitating audit readiness. In the pharmaceutical sector, in particular, it helps companies uphold product labeling and manufacturing standards, ensuring compliance with international trade regulations and reducing the risk of trade disruptions.
Moreover, document comparison software plays a pivotal role in adapting to post-Brexit medicine regulations by ensuring legal compliance, monitoring trade agreements, and mitigating risks associated with regulatory changes. Its ability to swiftly identify inconsistencies and compliance gaps makes it an invaluable tool for navigating these complex and highly regulated industries.
How to Ensure Medicine Compliance With Document Comparison Software?
Here’s how document comparison software can help in post-Brexit medicine compliance regulatory adherence:
The Future of Pharma and Brexit
Brexit has undeniably cast a shadow of uncertainty over the pharmaceutical industry, but it has also spurred innovation and adaptation. As pharmaceutical companies, healthcare providers, and patients navigate the complexities of medicine compliance, supply chain disruptions, and evolving regulatory frameworks, the resilience and determination of the industry to ensure access to safe and effective medicines remain unwavering.
While the full implications of Brexit on healthcare and pharmaceuticals are still unfolding, the commitment to safeguarding the health and well-being of patients on both sides of the English Channel remains of the highest importance.
The post-Brexit era presents an opportunity for the industry to demonstrate its adaptability and dedication to delivering vital medicines to those who rely on them. One way in which they can ensure this is through the implementation of efficient, streamlined, and error-free processes.
Implementing document comparison software in regulatory and quality assurance processes can help maintain medicine compliance, ensuring that documentation and pharmaceutical processes adhere to evolving healthcare regulations with complete ease while giving regulatory professionals peace of mind that no errors are slipping through.
Take a step in the right direction by setting up proper processes through document comparison software. Visit our Demo Center to learn more about our products at your own leisure and see how this technology can revolutionize your everyday business and regulatory practices.
How Document Comparison Software Improves Customer Experiences and Builds Trust
Date: November, 2023 | Category: Quality | Author: Hana Trokic
Imagine you are walking down the aisle at the drugstore and see a product that catches your eye. You pick it up to learn more about it only to find errors and inconsistencies on the packaging and labeling. How would you feel about the product? Would you trust that a company, that has so hastily brought this product to market, could actually produce effective and quality products?
Most likely, your interest in that product would completely diminish. What’s more, you most likely wouldn’t see yourself buying anything from that company and would question the legitimacy of its products.
This is because that one negative experience with that one product has led you to question your trust in the company and its whole production.
Businesses constantly seek ways to enhance customer experiences and build trust with their clients. With many different approaches, methods, and platforms to help them achieve their goal, technological solutions have emerged as a powerful tool that can significantly transform how organizations operate and interact with their customers.
Document comparison software is one of those powerful tools that helps ensure the accuracy of all products that go out to market – from the inside out!
Read on to explore how document comparison software is pivotal in revolutionizing customer experiences and fostering trust and brand loyalty.
The Significance of Customer Experience and Trust
Customer Experience is defined as a positive customer experience and is the foundation of customer loyalty. When customers have smooth, hassle-free interactions with a brand, they are likelier to return and recommend the company to others. Customer experience encompasses all touchpoints and interactions a customer has with a business, including communication, service, and product quality.
Continuous positive experiences with a brand lead to trust and, ultimately, brand loyalty. Trust is critical to any successful business relationship, as customers need to trust that a certain company and brand will deliver on its promises, protect their data, and provide value. Trust is earned through consistent, transparent, and reliable interactions.
Building Customer Trust with Document Comparison Software
Document comparison software, a crucial software for regulated industries that deals with critical content, has been found to also be extremely beneficial in other sectors due to its transformative impact on customer experiences and trust-building.
Here’s how this technology helps businesses achieve customer success:
Optimizes the Revision Process
Ensuring the accuracy of a product and its documentation is the first step to ensuring you are releasing a product that consumers will trust. This all happens during the revision stage of the product life cycle.
Document comparison software meticulously analyzes multiple versions of documents, and provides a comprehensive view of differences between files. This level of scrutiny ensures that errors are caught early, and inconsistencies are swiftly rectified.
The automated nature of document comparison software expedites the revision process, reducing the need for time-consuming manual inspections. Moreover, it facilitates collaboration among team members, allowing them to work concurrently on revisions while keeping track of all modifications.
As a result, organizations can streamline their revision processes, increase productivity, and maintain document accuracy and consistency, ultimately saving time and resources to pursue higher-quality outcomes.
Inaccurate or outdated information can lead to customer frustration and erode trust. Document comparison software ensures that all customer-facing content, such as packaging, labeling, marketing materials, and other critical documentation is accurate and can be updated accordingly with complete ease, without potential errors slipping through.
The use of document comparison software in quality assurance processes results in the reduction of errors and inconsistencies, and ultimately, reduces the potential for misinformation or miscommunication which could potentially foster mistrust in a company’s image.
Brings Trusted Products to Market Faster
The modern, fast-paced, global market leads consumers to expecting quick product releases, response to demand, and extremely fast service. Document comparison software accelerates document review and approval processes, enabling businesses to meet customer demands with speed and efficiency.
By automatically detecting and highlighting differences between various versions of crucial documents, the software helps minimize errors and streamlines the review and approval process, reducing the need for time-consuming manual checks.
Consequently, teams can make informed decisions swiftly, resolve discrepancies efficiently, and maintain compliance with industry standards, ultimately accelerating the product development cycle. In doing so, document comparison software not only enhances productivity but also instills confidence in the market, assuring consumers of the quality and reliability of the products they receive.
Document Comparison Software in the Real-World
Document comparison software is an extremely valuable platform for regulated industries that need to ensure the complete accuracy of their products. However, it also benefits a wide range of industries that want to ensure a positive consumer experience and build a strong and trusted brand.
Here is how document comparison software can benefit certain sectors:
Ready to Strengthen Your Brand?
Document comparison software is no longer just a niche tool; it’s a critical asset for any business looking to transform customer experiences and build trust. By promoting accuracy, streamlining communication, and optimizing processes, document comparison software empowers businesses to provide superior customer experiences that lead to long-lasting trust and loyalty. Embracing this technology is a strategic move for companies aiming to thrive in the digital age, where customer expectations are higher than ever before.
Looking to guarantee the trustworthiness of your brand? Take the first steps towards flawless customer experiences using GlobalVision’s state-of-the-art document comparison software. Begin experiencing the advantages of our cutting-edge software today.
Enhancing Your Verify Experience – Our Fall Release is Here
Date: October, 2023 | Category: Company | Author: Hana Trokic
Are you ready to heighten your Verify inspections and overall proofreading experience?
We’re thrilled to introduce significant improvements to Verify, designed to make the automated proofreading experience easier and more efficient. These product advancements have been rolled out in two waves throughout September and October!
With a substantial performance upgrade, a 69% improvement in Spell Check results and the addition of Single File Inspections, now called ‘Proofreader Mode’, our Verify Fall Release ensures your content is perfected, faster.
Additionally, this release marks a huge milestone for Verify’s core technology, as it has been completely rehauled and updated to an entirely new architecture with all modern technology—get ready to elevate your compliance review and inspection processes!
The Verify Fall Release also brings a number of major improvements and features including:
If you want to learn more about how to leverage these new features, book a demo of Verify here.
Upgraded Architecture, Upgraded Inspections
We’ve upgraded to an entirely new architecture with modern technology to offer you the best possible proofreading experience on the market. Though this upgrade brings with it many benefits and advantages, possibly the largest benefit is that it will increase development speed, resulting in highly requested features being released more rapidly.
This accelerated development pace translates to a high turnover of new features and capabilities, allowing regulatory and commercial experts to stay ahead of evolving compliance requirements by having the best tools available to them during their quality assurance processes.
The upgraded architecture also increases Verify’s reliability and uptime. This results in fewer interruptions to critical processes, where you can rest assured that your workflows run as smoothly as possible and with the utmost ease. In the exceptional instance of an issue occurring, the enhanced infrastructure ensures swift resolution, minimizing downtime and enhancing productivity.
Moreover, the optimization of our algorithms for faster inspections enables regulatory professionals and beyond to expedite their reviews, ensuring that all documents and critical content adhere to compliance standards with greater efficiency and precision.
This major breakthrough in Verify’s development empowers regulatory professionals and all automated proofreading users to work more effectively, maintain compliance, and improve the overall quality and reliability of their operations.
Boosted Responsiveness For Heightened day-to-day Efficiency.
Time is crucial when inspecting documents, especially for regulated industries where manual compliance procedures can sometimes hinder time-to-market
This new release brings a remarkable 15% improvement in responsiveness, backed by a more stable infrastructure to further help accelerate the revision cycle of critical content and ensure error-free files in record time.
Through this new upgrade, you can expect to load and inspect large files faster than ever, without rendering issues, decreasing delays in inspections and allowing for an overall more seamless inspection.
Save More Time With Built-in Spell Check Rules
The new fall release also brings with it new built-in rules that improve Spell-Check results by 69%. The new update will only flag important spelling errors, ensuring a more efficient review process.
This means the software no longer detects terms such as URLs or words containing numbers as spelling errors allowing teams to focus their energy on more crucial aspects of their inspections without getting set back by minor details.
The improved Spell Check feature also assists regulatory professionals in meeting FDA requirements by ensuring accurate, clear, and error-free documents. This helps maintain compliance with FDA guidelines, reduces legal and reputational risks, and promotes efficiency.
Single File Inspection For Ease and Simplicity
We’re simplifying the inspection process with the introduction of a Single File Inspection capability called “Proofreader Mode”. This feature allows you to upload and inspect a single file when there is no need to compare it against a source file. This feature is particularly beneficial for regulatory professionals who have many documents to review and need to optimize their entire process.
The upgrade was designed to facilitate Barcode Inspections and Spell Checks, and Braille Inspection. Previously, the software required that two identical files be uploaded to perform an inspection. Now, you can tackle these tasks with precision and ease, one file at a time.
More Review Enhancing Features
If those upgrades are not enough to bring your compliance reviews to the next level, regulatory and commercial professionals can expect to enhance their inspections through the following features:
A Better Verify Experience
With Verify’s fall release and a complete overhaul of our core technology, you will experience a more responsive and stable platform. With the addition of the many features and functionality presented, regulatory and commercial professionals tasked with reviewing content for total compliance lifesciences can perfect their content, faster.
These exciting updates to Verify are a testament to our commitment to improving the overall user experience and making quality inspections more efficient and effective.
For more detailed information about our latest upgrades, read the Release Notes, and, make sure to watch our informative video, which highlights some of the new additions to the Verify fall release.
If you haven’t experienced the time-saving and compliance enhancing powers of Verify yet, get started today with a Free Trial.
A Definitive Guide to Data Integrity Assurance
Date: October, 2023 | Category: Compliance | Author: Hana Trokic
In the digital age, where data serves as the backbone of decision-making, business operations, and technological advancements, ensuring the integrity of data has become paramount.
From sensitive information to critical corporate records and beyond, the accuracy, consistency, and reliability of data play a pivotal role in building trust, driving innovation, and avoiding potentially catastrophic consequences.
This comprehensive guide is designed to unravel the intricate layers of data integrity, offering insights into its significance, the challenges it poses, and, most importantly, the proven strategies and best practices that individuals and organizations can adopt to safeguard their data.
Whether you’re seeking to refine your enterprise’s practices, you’re a small company that is eager to improve its systems and security, or personally looking into how you can secure your data and privacy, this guide is your compass in navigating the complex landscape of data integrity assurance.
What is Data Integrity?
At its core, data integrity represents the steadfast accuracy and consistency of information throughout its lifecycle. It encompasses the assurance that data can be either valid, invalid or in the process of becoming valid.
Error-checking and validation processes are methods often used to ensure data integrity and it’s easier to think of it as the trustworthiness of a digital asset, where any modifications, corruptions, or unauthorized changes are effectively prevented or quickly detected and corrected.
In essence, data integrity is the pillar on which sound decision-making, seamless processes, and reliable systems are built. It not only guards against accidental errors and technical glitches but also shields against intentional tampering, ensuring that data retains its value and authenticity, fostering confidence among stakeholders and enabling a strong foundation for operational excellence.
The key to a successful software development lifecycle? Data integrity. Read more here!
Why is Data Integrity Important?
Data integrity is a cornerstone of modern information-driven landscapes, playing a pivotal role in upholding the credibility and effectiveness of any data-driven endeavor.
In a world where organizations and individuals rely on data for critical decision-making, strategic planning, and innovation, the importance of data integrity cannot be overstated.
Maintaining data in its accurate, unaltered state ensures that insights drawn and actions taken are based on a foundation of truth, enhancing the reliability of outcomes. Moreover, data integrity is a foundation of regulatory compliance, particularly in industries handling sensitive information such as healthcare and finance, for example.
Without robust data integrity measures, the risk of errors slipping through, compromised security, and a damaged brand image pose a large threat. By creating a culture of data integrity, organizations foster trust among stakeholders and customers while driving efficiency in operations and securing their ability to navigate the complexities of the digital age with confidence.
Data Integrity Best Practices
When it comes to ensuring data integrity, there are several fundamental principles that serve as the foundation for maintaining the reliability and trustworthiness of your data.
These principles are collectively known as ALCOA, an acronym that stands for Attributable, Legible, Contemporaneous, Original, and Accurate.
What Are Threats to Data Integrity?
The landscape of data integrity faces a multitude of threats that can compromise the accuracy, reliability, and trustworthiness of information. Malicious cyberattacks, ranging from hacking and phishing to ransomware, pose a significant danger by potentially altering or stealing data.
System glitches, hardware failures, and software bugs can inadvertently introduce errors and inconsistencies. Data entry mistakes, often attributed to human error, can distort information at the point of creation.
Additionally, as data travels through various stages of its lifecycle, data integrity risks emerge during storage, transmission, and processing. Moreover, inadequate data governance and insufficient security measures can create vulnerabilities that malicious actors exploit.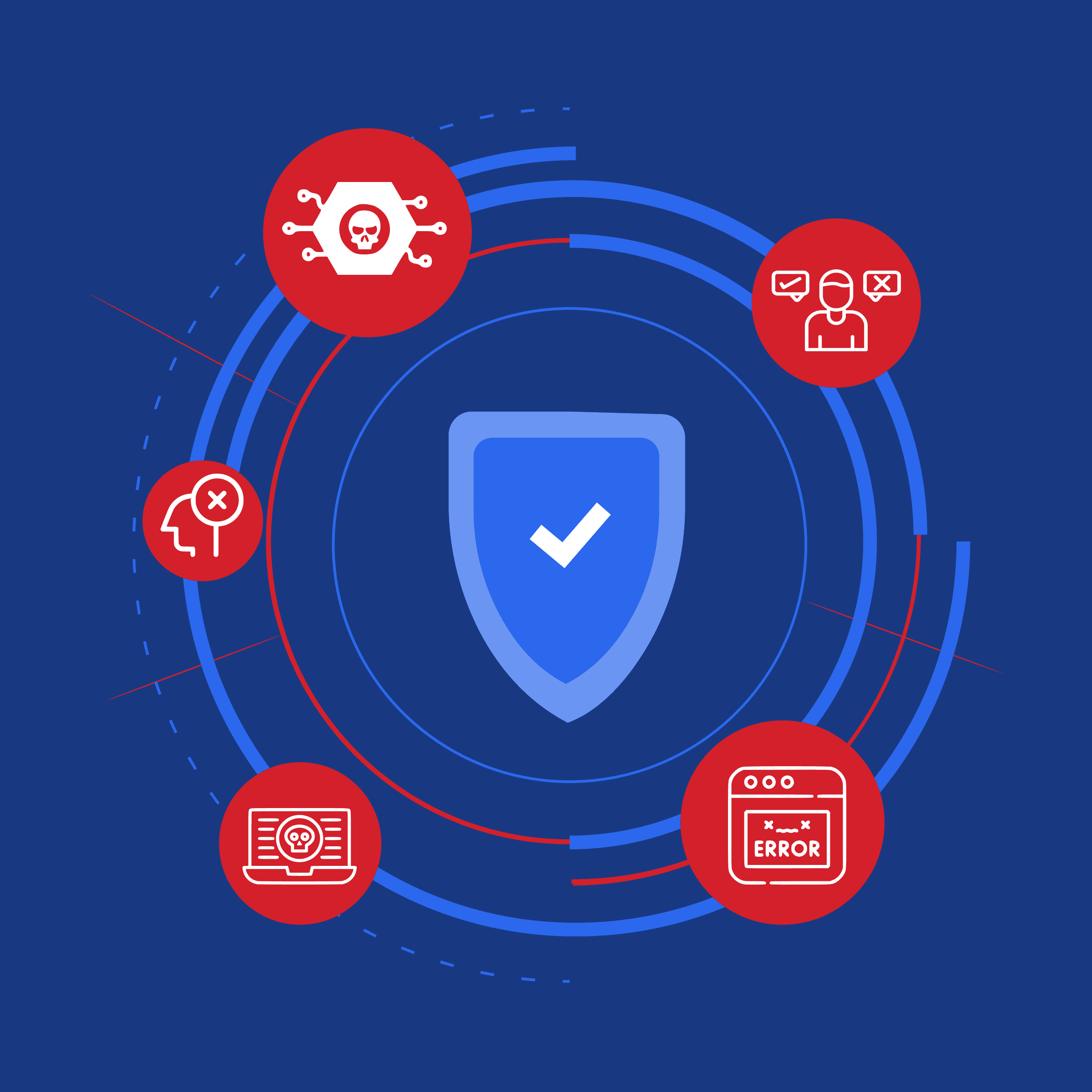
These threats collectively highlight the necessity of robust data integrity measures that encompass technological safeguards, employee training, vigilant monitoring, and stringent compliance with established protocols.
Overall, threats to data integrity can appear in many different forms. Some of the most common threats, however, are often internal. Examples include:
How to Minimize Data Integrity Risks
In today’s marketplace, individuals and companies need to feel confident that there is no loss of quality when using computer systems. To accomplish this, there are effective strategies that companies may implement to manage their data integrity risks and ensure their data respects the ALCOA principle. By moving from a reactive to a proactive way of thinking, the following key requirements and controls may be put in place to ensure data integrity and minimize risks.
For more information about how you or your organization can ensure complete data integrity, read our detailed blog post.
Top Backup Strategies to Keep Data Integrity Intact
Just backing up data isn’t enough to keep data intact anymore. While it’s a necessary step and a good start, a backup means little if there aren’t adequate safeguards in place to protect the integrity of the data that might have to be recovered.
Even if backups themselves are a safeguard, they must be seen as an asset in their own right. After all, it’s estimated that 100 MB of company data is worth $1 million on average. Half the firms that cannot recover lost data in 10 days cannot recover themselves.
That is why, it is in every individual’s and company’s interest to have a good backup plan and strategy in place. Here are some backup strategies to keep data intact:
To find out more about best practices and top-back-up strategies to keep your data integrity intact, read our in-depth blog post.
How to Reduce Data Integrity Risks for Regulated Industries
In regulated industries, reducing data integrity risks is paramount to ensure compliance and maintain public trust. By implementing stringent data management protocols, conducting regular audits, and fostering a culture of transparency and accountability, organizations can effectively mitigate data integrity risks and uphold regulatory standards.
Here are some ways businesses in regulated industries can overcome data integrity issues:
For a step-by-step look at how you or your organization can ensure data integrity, read our in-depth “12 Ways to Reduce Data Integrity Risks for Regulated Industries”
The Role of Document Comparison Software in Ensuring Data Integrity
As automation technology becomes increasingly prevalent and the use of different software, applications, and the internet becomes an absolute necessity, data integrity is as important as ever. Not only does it serve as the driving force behind technology of all forms, but it also acts as a fail-safe.
Document comparison software is one viable way to catch and stop errors that risk corrupting data in their tracks. The software is designed to compare two or more documents to identify all differences, changes, and errors between them allowing for ease of proofreading, and editing and ultimately leading to error-free content. As previously mentioned, this type of software is particularly useful in industries that deal with highly regulated and critical content.
Here are some ways document comparison software can help ensure data integrity:
Enhances Security
While data security is different than data integrity, the two go hand in hand. Like data quality, data security is a single facet of data integrity (but not vice versa). Nevertheless, without the proper degree of security, data can become compromised due to breaches, among other threats. In other words, for data to have integrity, it must first be secure.
As a result, document comparison software can be considered a key component of any complement of tools designed and implemented to enhance the security of data. Errors are simply outliers or anomalies, which are defined as observations that lie outside of norms Document comparison software can build baselines of systems, their users, and the data they create, leading to the easy detection of behavioral deviations, whether there is malicious intent or not.
Do you think following FDA data integrity guidelines is hard? It’s way easier than you think!
Reduces Human Error
There’s an inherent risk whenever you rely on human resources. There are some things a machine will likely never be able to do as well, but analyzing data is not one of them. It’s similar to the situation with manual proofreading, where, the longer the process is, the less likely errors are to get caught. Fatigue sets in eventually and the effectiveness of proofreaders declines over time.
In much the same way, the automated analysis of unstructured data saves time, thereby improving the overall efficiency of the process. Employees wouldn’t be replaced, either. There would still be a need to oversee the analysis. The right document comparison software would all the while keep relevant parties apprised of how the data behaves.
Interested in learning more about how document comparison software can help ensure data integrity? Read more here!
Prevents Issues from Recurring
It isn’t just the current errors the software might catch, but the ones in the future that would otherwise slip through the cracks. Consider document comparison software as an example. A form of error-detection software, GlobalVision features an audit trail for compliance with FDA 21 CFR Part 11.
The platform doesn’t just go over the document pixel-by-pixel or character-by-character to detect graphics and text differences (among other types). The application tracks parameter changes and log-ins, so data becomes “attributable,” one of the five principles of data integrity.
Read about how GlobalVision Adds Electronic Signatures for Enhanced Data Integrity to the Most Comprehensive Platform Yet!
The Importance of an Audit Trail to Securing Data Integrity
Though the word might spring negative connotations, audits are an unavoidable part of life for many corporations that bring many benefits to daily functions and processes.
In essence, trails are the lists of transactions or events kept track of to help auditors and, in many ways, those being audited as well. An audit is simply an investigation of accounts and records in general.
For example, audits can be key to achieving and maintaining regulatory compliance, which is in turn critical to operating in regulatory sectors. It is also important to note that external and internal audits are to be expected on a regular basis.
External vs. Internal Audits
External audits and internal audits serve different purposes:
The Benefits of an Audit Trail
Regardless of the focus of an audit, trials are undeniably critical to their success. And success is what all parties should strive for, whether they’re doing the auditing or being audited.
Audits can be made easier if all required records have been kept and are easily accessible to auditors. Automated trails that are easily searchable make smooth audits more of a reality.
Trails are theoretically included in the software as one of many required technical controls that enable users to achieve compliance with 21 CFR Part 11 with the Food and Drug Administration (in the United States; equivalent to Annex 11 in the European Union).
Compliance here ensures companies implement good business practices through reliable electronic records, which must be able to be accurately displayed and exported. Here, the audit trail serves to log what changes to application data were made, when, and by whom and be available for review.
Whoever ends up conducting that review, whether it’s an agency or the company itself, the auditor will no doubt thank you as the bigger picture begins to take shape. Identifying the individual trees is key to seeing the forest as a whole, though. Finding your way through can be hard, but an audit trail can clearly reveal the right path to take.
Read more about the importance of an audit trail to securing data integrity here.
Step Up Your Data Security
Data integrity serves as the pillar for informed decision-making, operational efficiency, and regulatory compliance.
By delving into the significance of data integrity, the principles of ALCOA, threats to data security, and practical strategies for safeguarding it, this guide equips individuals and organizations with the knowledge and tools necessary to protect their data assets.
Whether you are an individual seeking to secure your personal information or a business aiming to strengthen your operations and brand, the principles and practices outlined provide a compass to navigate the complexities of the digital age with confidence.
As data continues to evolve and become more integral to our lives, the assurance of its integrity remains vital, ensuring that our digital assets are built on strong foundations of truth, trust, and reliability.
Ready to upgrade your data security? Take a step in the right direction by setting up proper processes through automated quality control. Request a demo of our innovative proofreading software and see how this technology can revolutionize your everyday business practices along with your data security.
_________________________________________________________________________________________
Did you enjoy reading this post? Check out these other related post: