Date: May, 2017 | Category: Company | Author: Jonathan Hou
You see the words “web,” “cloud,” and “internet of things” just about everywhere you go these days. In today’s digital age, where “there’s an app” for almost everything, you probably wouldn’t last even 10 minutes without hearing something about the internet.
But how could you not, when technology has become an integral part of our everyday lives.
With the mainstream accessibility of broadband Internet and 4G, users can access their favorite web-based and mobile applications wherever and whenever they want. However, not all applications are created equal and the convenience afforded by the internet has different levels attached to it. Other factors like affordability and security considerations appear at the forefront of the ongoing debate between web-enabled and web-based applications.
Web- Enabled Vs. Web-Based
Web-Enabled
There is an inherent advantage to this approach. IT departments can provide employees with remote access to older, legacy programs to maximize the return on investment on specialized applications deployed across the company.
Those same applications may be firmly entrenched within the organization as key components, mission-critical to its processes and subsequent successes.
That ROI takes a hit though with added costs of maintaining a whole Citrix environment, not to mention all the extra network bandwidth usage from streaming video-like graphics across the web.
Often, it requires a client plug-in (ActiveX) control to be installed in the background. Plus, integration with web-based systems remains limited because the program in question is still just a desktop application, after all… albeit with extra layers tacked on to enable functionality over the internet.
There are also security risks with incorrectly implemented Citrix servers; Since remote desktop access to Citrix servers requires different permission levels for different users, there is the potential for unauthorized access to certain files on a Microsoft Windows file server.
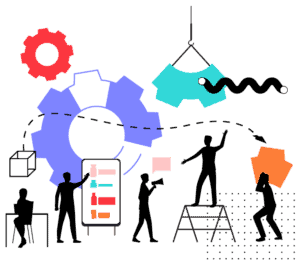
Web-Based
Meanwhile, one disadvantage is the required standardization of browsers across the company to ensure a consistent user experience. Another is the web in general to ensure a user experience, to begin with. Whereas web-enabled applications are based on desktop versions, web-based applications are based on, well, you guessed it, the internet! If the internet goes down, so too does the app.
That being said, a functioning internet connection is pretty much a prerequisite to running a business these days, and web-based applications are generally considered to be more cost-effective relative to their web-enabled cousins, as the application runs directly in a browser.
Furthermore, the applications themselves only need to be installed and updated on a single host server instead of on each workstation, which also means tighter security, and not having to focus on countless systems (as far as the single application is concerned).
Web-based applications can be hosted by the vendor, as in the classic Software-as-a-Service model, or the client, with several potential arrangements out there. This plays further into the notion that the web-based approach benefits from superior flexibility. Up-front and subscription-based pay schemes exist (although, in terms of hard cash doled out, both tend to even out over time).
Another advantage is that web-based applications can integrate near-seamlessly with the vast ecosystem of other web apps such as Salesforce CRM, Documentum, and cloud-based storage because they are cut from the same technological cloth.
With the growing trend of mobile devices being used as means to access apps remotely, research firm Gartner declared heading into 2015 that cloud and mobile computing will keep on converging, promoting the development of centralized applications for use anywhere. That sounds awful like a bet on “web-based” moving forward. A few years later, nothing has dispelled the argument that it’s more of a future-proof option… if you’re in the position to have an option between the two, anyway.
For more information on this constant debate, please visit:
→ Web-Based Vs. Web-Enabled Software
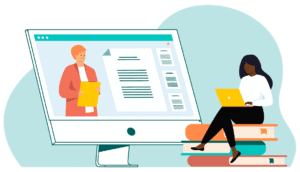
Which Application is Better?
Sticking with the mobile device example, deciding between a web-enabled application and a web-based application is like deciding between smart and flip phones. Both can make calls, but you gain access to a much larger ecosystem of integrated apps with your smartphone’s newer technology.
Everything may be headed in the same direction, and web-enabled and web-based applications each take you from Point A to Point B. However, it’s Points C-Z that are the issue. Roads are opening up as we speak and a trusty 18-wheeler representing web-enabled applications might not be able to fit through tunnels out of town. Not like a sleek, mobile-device-friendly sedan anyway.
GlobalVision however, offers both versions of its market-leading automated proofreading technology.
For those who prefer their desktop application, there’s GlobalVision Desktop (GVD). Built for use in production environments, GVD combines powerful inspection tools into one robust application – so you can be sure your files are accurate as they move along the quality workflow.
However, for those who prefer to work on a cloud, web-based application, our latest and most innovative proofreading technology Verify is just for you.
Created for regulated industries, Verify is GlobalVision’s inspection technology reinvented. Verify ensures a seamless and convenient end-user experience, delivering superior inspection results, in a cloud-based, innovative software.
Learn more by requesting a demo of GlobalVision here or try our web-based proofreading software, Verify, for free!
GlobalVision is the leading developer of quality control technologies. Learn how GlobalVision has provided new business opportunities across all industries with an extra layer of security.
Request a free trial for GlobalVision Digital Inspection Solution
Learn More about the Actual Difference Between Quality Control Inspection Apps
Harmonizing Medical Device Package Labeling Across Markets
A picture is worth a thousand words. This is especially true in the Medical Device Packaging and Labeling industry. Symbols are an important tool to harmonize medical device packaging labels across markets worldwide, save valuable space while sharing important information and guidelines, and save in translating costs.
In order to minimize misinterpretation across markets, symbols have standards in different regions. This graphic shows some of the most common symbols under ISO 15223 and EN 980.
There are seven main symbol categories– Manufacturer Symbols, Storage Symbols, Safe Use Symbols, Sterility Symbols, IVD Specific Symbols, Transfusion Symbols and Others.
1. Manufacturer Symbols
This category includes any symbol with the product’s manufacturing. It can include when it was made, where, and any product identification data, fall into this category.
2. Storage Symbols
When storing medical devices, elements such as temperature, humidly, and exposure must be considered. These symbols are extremely important to maintain the integrity of the device.
3. Safe Use Symbols
Safe use symbols are warnings to reduce risk to the users. These symbols can significantly reduce the risk associated with many medical devices.
4. Sterility Symbols category
Sterility symbols communicate important information pertaining to the sterile conditions of the product. This could mean how they were sterilized, or warning about conditional use.
6. IVD Symbols
IVD symbols are specifically used on in vitro diagnostic devices and communicate information germane to those product types.
6. Transfusion Symbols
Used on devices that are involved in the transporting of fluids from one place to another.Used on devices that are involved in the transporting of fluids from one place to another.
7. Others
The patient number is the only symbol that falls into the other category.
GlobalVision is the leading developer of Automated Proofreading technology for the pharmaceutical industry. Learn how GlobalVision has helped top Pharmaceutical Companies in quality control.
Request a free trial for GlobalVision Digital Inspection Solution
Learn More about the Medical Spell-Checker and Pharma Dictionary
You’ve Got Questions? The GlobalVision Help Center Has Answers.
You may have already noticed the sleek, revamped look of the GlobalVision website. It’s since extended to our brand-new, easy-to-use Help Center, which provides users with all the know-how they need to get the most out of their automated quality control software. It comes fully equipped with all the fixings you’d expect to ensure any knowledge you require go smoothly.
All in One Place
In-depth blog entries and regularly posted instructional videos detail tips and tricks on using and your GlobalVision software. Community forum access meanwhile offers up the opportunity for you to discuss GlobalVision products and best practices with customers just like you or to provide us with feedback, whether it’s positive or something that can be improved upon in a future release.
We’re always looking for ways to improve upon our products and ready to help you through any issues you might encounter. You can also leave us a message by clicking on the box at the bottom of your screen. Resolving any issues you may have is our highest priority.
Create your account
You can even track individual tickets that you open through the revamped My Requests feature. It’s all as simple as first creating an account, then submitting a ticket, and finally clicking to track it. To create an account:
File Tickets Online
To file a ticket, you can either click at the bottom of the Main page or the “Contact technical support” link in the footer of any page. That launches the Support Request form. When you’ve filled out all the required fields, just click Submit Support Request.
Even without an account, you can file a ticket by following the steps immediately above. However, if you’d like to track its progress, you need to be logged in first. Once the ticket is submitted, click on your name in the top right-hand side and select My Activities from the drop-down menu. Any updates to comments you’ve made on articles or topics are visible too.
It all comes back to the GlobalVision community, of which you’re a part. You’ve got a say too. We’re here to listen.
Learn More about Quality Control’s Best-Kept Secrets
5 Ways to Minimize Issues While Preparing Artwork for Box Packaging
Date: June, 2017 | Category: Proofreading | Author: Devine Barroga
The process of preparing artwork is essential for box packaging. There is a considerable amount of detail that goes into preparation, but it doesn’t have to be a frustrating ordeal.
PakFactory has put together a series of practices to help customers and companies minimize artwork issues during the manufacturing process and increase efficiency all the while.
How to minimize issues during this process? Here are 5 ways to minimize issues in packaging artwork production.
1. Finalize Your Artwork Specifications
Having the required specifications means having the exact dimensions, material, printing, and coating from your customers. If these details aren’t sorted out properly, you may face timing challenges once you arrive at the artwork stage.
This doesn’t necessarily affect the artwork directly, but it should be handled with care. Depending on the time frame of your packaging project, preparation can become rushed if this isn’t established from the beginning.
Imagine having to change the dimensions when already at the artwork stage. Depending on the revisions, it can potentially alter the packaging’s specifications — from material and coating to even structure. In this case, you would need to start over again.
2. Dieline Preparation
This is one of the most crucial parts of the process of preparing your artwork for packaging. The dieline is the main template (or outline) in which your artwork will be placed and is required when producing the physical output.
The dieline creation process requires specific details so that the physical form of the box can be produced. Surprisingly, designers can miss some of them.
There are two ways to avoid dieline problems:
3. Work in CMYK Color Space
Once you have your dieline finalized, it is time to set up your artwork. Another problem that designers encounter revolves around uploading the artwork onto the dieline. There are times when customers receive their packaging and aren’t too happy with the colors, as they don’t match what they see on the screen.
In this case, the problem is that designers sometimes forget to convert their color modes. The correct color mode for printing is CMYK. Therefore, when uploading and creating your artwork, it needs to be under a CMYK color space. Creating the artwork in RGB and printing it on the box will have a significant effect on color appearance.
4. Prototyping Artwork Packaging
Another way to minimize artwork issues before production starts is by creating a prototype. This lets you see the exact packaging from the structure to the exact colors and finishing. Seeing the prototype up close makes it easier to spot color mistakes or any elements that need to be changed.
5. Artwork Approval Process
A company’s artwork approval process can make a difference in reducing issues encountered during the project as well, especially when a physical prototype isn’t produced.
If you have a manufacturer that goes through several approval cycles (along with a digital, CTP, or 3D rendering proof), you are in good hands. It is important that you undergo several approval processes to make sure any artwork issues are spotted before production gets underway. This will save a lot of time and money.
Remember to get the details right the first time. The extra effort will be worth it. By following these tips, you’ll be on your way to creating stellar box packaging and helping to reduce packaging errors in the future.
GlobalVision is the leading developer of proofreading technologies for the print and packaging industry. Learn how GlobalVision has provided an All-in-One Quality Control for Error-Free Printing
Request a free trial for GlobalVision Digital Inspection Solution
Learn More about How to Avoid Waste on the Print Production Floor
How to Avoid Complete Medicine Recalls due to Labeling Errors
Date: May, 2017 | Category: Proofreading | Author: Marvin Magasura
The Pharma industry is by far the most demanding industry when it comes to packaging quality control. The processes, rules, and regulations are extremely complex and must be adhered to.
Unfortunately, because many companies still implement manual packaging and label artwork inspections, these results are often prone to human error, which is the most common cause of complete recalls due to labeling errors.
Although recent changes in packaging and labeling are pointing in the direction of process automation, a huge percentage of large companies are not there yet. This is due to the fact that human resources have a hard time adapting to a workflow change if the new process hasn’t been clearly defined.
Here are some tips for avoiding complete medicine recalls due to labeling errors.
Define the Change Process and New Packaging Quality Control Workflow Clearly
Switching from manual to automated may sound easy, but if the department team members don’t have the required technical knowledge, the process can be slowed down radically. What was supposed to be the solution to avoiding labeling errors, becomes the cause of it.
This is why it’s crucial to train the entire department staff in the use of process automation tools. Additionally, integration into the existing workflow, so only minor changes are made, and process automation SOPs are the best methods to help team members maximize the benefits of the change, succeed in avoiding packaging label recalls because of errors, and speed up the process from months to days.
Reports at Each Stage of Label Production
Generating reports at each stage of the label production and quality control processes and approvals help compare current and prior job versions. These reports should show the changes made during the exchange; who made them and the label errors which may have occurred between a master and a sample design and text.
Reports are also crucial at the point at which the master job has been sent to the printer or the printing supplier. They enable final verification to ensure that error-free labels are being sent to the printer.
Inspecting the Artwork at Every Step of the Label Production
As already mentioned, rules and regulations covering packaging quality control in the pharma industry are very strict. This is obviously because patient safety is at stake, along with brand compliance to fulfill the demands of the regulations.
Companies often use different tools for packaging artwork production and quality control. All parts of the artwork must be inspected. These include parts such as; text, labels, design, braille content (required on pharmaceutical packaging), and barcodes.
Often, many companies inspect some or most of the parts manually. This practice has shown itself as ineffective, inefficient, and risky. It may take hours to verify some of the parts of the packaging labels and the job often goes through many team members. This kind of inspection setup opens the door to the occurrence of labeling errors.
Automation Technology Advancement
Packaging quality control automation technologies have evolved over recent years. Today it is possible to integrate an all-in-one quality control platform into your production process and workflow so that at each stage of the production, inspection is implemented via software tools and printing inspection hardware.
This includes inspection of text, spelling, artwork graphics, braille text, barcode, pre-print, and print.
A good packaging quality control software platform should adhere to the rules and regulations of the pharma quality control standards. It should be able to read and inspect various formats and compare different formats to each other.
In other words, a pre-print proof job has to be comparable to a digital format in the form of an image, text, or graphic.
Finally, an automation platform for packaging quality control should guarantee a maximum return on investment, maximum time efficiency, and maximum risk reduction in terms of eliminating labeling errors.
GlobalVision is the leading developer of quality control technologies for retail and pharmaceutical packaged goods. Learn how GlobalVision has provided new business opportunities across all industries with an extra layer of security.
Request a free trial for GlobalVision Digital Inspection Solution
Learn More about How to Stop Label Recalls in Your Supply Chain
Learn how to adhere to FDA labeling requirements with complete ease. Your Complete Guide is here!
Why “Web-Enabled” Apps Aren’t Really Web Apps
Date: May, 2017 | Category: Company | Author: Jonathan Hou
You see the words “web,” “cloud,” and “internet of things” just about everywhere you go these days. In today’s digital age, where “there’s an app” for almost everything, you probably wouldn’t last even 10 minutes without hearing something about the internet.
But how could you not, when technology has become an integral part of our everyday lives.
With the mainstream accessibility of broadband Internet and 4G, users can access their favorite web-based and mobile applications wherever and whenever they want. However, not all applications are created equal and the convenience afforded by the internet has different levels attached to it. Other factors like affordability and security considerations appear at the forefront of the ongoing debate between web-enabled and web-based applications.
Web- Enabled Vs. Web-Based
Web-Enabled
There is an inherent advantage to this approach. IT departments can provide employees with remote access to older, legacy programs to maximize the return on investment on specialized applications deployed across the company.
Those same applications may be firmly entrenched within the organization as key components, mission-critical to its processes and subsequent successes.
That ROI takes a hit though with added costs of maintaining a whole Citrix environment, not to mention all the extra network bandwidth usage from streaming video-like graphics across the web.
Often, it requires a client plug-in (ActiveX) control to be installed in the background. Plus, integration with web-based systems remains limited because the program in question is still just a desktop application, after all… albeit with extra layers tacked on to enable functionality over the internet.
There are also security risks with incorrectly implemented Citrix servers; Since remote desktop access to Citrix servers requires different permission levels for different users, there is the potential for unauthorized access to certain files on a Microsoft Windows file server.
Web-Based
Meanwhile, one disadvantage is the required standardization of browsers across the company to ensure a consistent user experience. Another is the web in general to ensure a user experience, to begin with. Whereas web-enabled applications are based on desktop versions, web-based applications are based on, well, you guessed it, the internet! If the internet goes down, so too does the app.
That being said, a functioning internet connection is pretty much a prerequisite to running a business these days, and web-based applications are generally considered to be more cost-effective relative to their web-enabled cousins, as the application runs directly in a browser.
Furthermore, the applications themselves only need to be installed and updated on a single host server instead of on each workstation, which also means tighter security, and not having to focus on countless systems (as far as the single application is concerned).
Web-based applications can be hosted by the vendor, as in the classic Software-as-a-Service model, or the client, with several potential arrangements out there. This plays further into the notion that the web-based approach benefits from superior flexibility. Up-front and subscription-based pay schemes exist (although, in terms of hard cash doled out, both tend to even out over time).
Another advantage is that web-based applications can integrate near-seamlessly with the vast ecosystem of other web apps such as Salesforce CRM, Documentum, and cloud-based storage because they are cut from the same technological cloth.
With the growing trend of mobile devices being used as means to access apps remotely, research firm Gartner declared heading into 2015 that cloud and mobile computing will keep on converging, promoting the development of centralized applications for use anywhere. That sounds awful like a bet on “web-based” moving forward. A few years later, nothing has dispelled the argument that it’s more of a future-proof option… if you’re in the position to have an option between the two, anyway.
For more information on this constant debate, please visit:
→ Web-Based Vs. Web-Enabled Software
Which Application is Better?
Sticking with the mobile device example, deciding between a web-enabled application and a web-based application is like deciding between smart and flip phones. Both can make calls, but you gain access to a much larger ecosystem of integrated apps with your smartphone’s newer technology.
Everything may be headed in the same direction, and web-enabled and web-based applications each take you from Point A to Point B. However, it’s Points C-Z that are the issue. Roads are opening up as we speak and a trusty 18-wheeler representing web-enabled applications might not be able to fit through tunnels out of town. Not like a sleek, mobile-device-friendly sedan anyway.
GlobalVision however, offers both versions of its market-leading automated proofreading technology.
For those who prefer their desktop application, there’s GlobalVision Desktop (GVD). Built for use in production environments, GVD combines powerful inspection tools into one robust application – so you can be sure your files are accurate as they move along the quality workflow.
However, for those who prefer to work on a cloud, web-based application, our latest and most innovative proofreading technology Verify is just for you.
Created for regulated industries, Verify is GlobalVision’s inspection technology reinvented. Verify ensures a seamless and convenient end-user experience, delivering superior inspection results, in a cloud-based, innovative software.
Learn more by requesting a demo of GlobalVision here or try our web-based proofreading software, Verify, for free!
GlobalVision is the leading developer of quality control technologies. Learn how GlobalVision has provided new business opportunities across all industries with an extra layer of security.
Request a free trial for GlobalVision Digital Inspection Solution
Learn More about the Actual Difference Between Quality Control Inspection Apps
How a Little Error Can Ruin a Great Design
Our world is growing at a rapid pace and so is the consumer market. The space between the market and the consumer’s home has drastically shrunk in the recent times, with online marketplaces as the next big thing. Customers can easily book, order and buy different items from all around the world—and get it delivered directly to their homes.
In such a crowded space what do you think catches the eye of your target audience?
Well, these are a few factors that influence a person to buy your product. And that is why, as a designer, you must try vigilantly to avoid little errors—because those small mistakes can ruin a great design and an amazing product.
A few design errors, like the following, can ruin an otherwise well-made design:
Not Understanding the Product and the Target Audience
This often happens when different teams handle various aspects of the development of the product. And more than often it happens that the designing team doesn’t fully understand the product, so the end design doesn’t fully or properly convey the product to the target audience.
Way back in 1997, the now famous animation cartoon The Pokemon was banned after 700 children around Japan suffered from various ailments. Some of the children experienced blurred vision, a few passed out and many complained of nausea. Some extreme cases were reported where the children suffered seizures and temporary blindness.
What caused all this?
Well, in the episode called “Electric Soldier Porygon” there was a scene where Pokemon strikes lightning, and the screen goes all blue and red for some time. This lightning effect triggered “photosensitive seizures” in the children, and one in every four thousand children suffers.
The episode was banned and was never broadcasted anywhere in the world again.
How can designers avoid such mistakes?
Designers must have knowledge of the product as well as the target audience, and and what might trigger a negative or positive behavior in them. For example—simple understanding of color psychology would have prevented The Pokemon episode ban entirely.
Using the Wrong Typography and Font Overload
Designers always play with fonts and typography, and font design and size are one of the most important parts of any print or online media. The key is to maintain the perfect balance and not overdo it.
A design is not about arranging pretty looking fonts and merely being pleasing the eye of the consumer; it’s also important to grab their attention and speaking directly to them. Any fonts used in a design must blend well with not only the background but the overall message the brand wants to deliver.
Check out some of the top fonts for packaging design.
Not Saving Files in the Correct Format
Amateurs might not have much experience or professional training, but companies often hire them to create designs in order to save some money. But what many beginners fail to remember is that saving files in the correct format is as essential as the design itself.
Usually, most of the print work is saved in CMYK format with 300 dpi, and most of the web work has to be saved in RGB. If not saved in the correct format then the final print might not be as clear as expected, and in turn it can end up ruining all your printed material.
Readability and Spellings
Let’s understand one thing here: designers are not copywriters. They mess up spellings and misuse words. To avoid these types of mistakes, proofread all the documents—and the best way to proofread can be to use proofreading software or spelling inspection tools.
You can also avoid readability problems and spelling errors by asking someone else read it or hiring a professional. A fresh eye will always catch more errors than the designer can.
These were some of the errors that commonly occur and can be avoided easily. And while they might seem harmless, if these mistakes are not taken care of early on then it might ruin the finished design completely. In a time when consumers crave impeccably-designed products and want to stay constantly updated with the latest offering in the market, a miniscule error can not only ruin your design but also hurt your sales.
Guest post by Marvin Magursara,
SEO Manager, GlobalVision
Marvin Magusara studied Robotics Engineering at UWE Bristol and is currently an SEO manager at GlobalVision, a company that provides machine vision software technology for quality control in packaging inspection.
His speciality field of Digital Marketing is SEO. He is currently working as an SEO consultant for a variety of companies.
Marvin is also an entrepreneur; he’s the founder of Graftene, a Web Agency and BubbleLocal SEO.
Due to his obsession with SEO, he spends most of his working hours doing SEO and content marketing, and writing for notable blogs in the marketing sphere.
GlobalVision is the leading developer of proofreading technologies for retail and consumer packaged goods. Learn how GlobalVision has helped Consumer Goods companies of all sizes in quality control.
Request a free trial for GlobalVision Digital Inspection Solution
Learn More about How Can Printed Manuals Improve Your Staff Training
Big Pharma Pokes Its Head in the Cloud (Finally)
Known for keeping their cards close to their vests to prevent other players from sneaking a peek, drug companies waited until the last possible moment to move to the cloud. Now sufficiently satisfied that their security concerns have been addressed, they’re finally poised to reap the benefits.
Positive Side-Effects
The advantages the cloud offers are wide-ranging. They run the gamut from facilitated corporate communication between teams in different parts of the world to lower operational costs, both of which are to be expected to a certain extent. They are arguably even interconnected as increased collaboration can help lead to streamlined operations.
However, other benefits aren’t as obvious. These include the flexibility of a scalable IT infrastructure (we’ll get to that later on), and, yes, even increased security. That would be through a variety of measures like encryption, cloud data protection gateways, and hybrid setups, which allow companies to store confidential data on private clouds.
Security concerns within the industry were in part due to required compliance with laws and regulations such as those enacted by the Health Insurance Portability Act. They’re also in part due to best practices, which logically state that sensitive, proprietary information should be protected much like cubs would be by a grizzly bear.
However, as has long been established, if done right, cybersecurity should present no more of an issue than implementing proper physical security measures would in the real world. There is a natural apprehension to deviate from what has been the norm for decades, but the reality is the cloud can be more secure than a brick-and-mortar fortress of a casino, and, it should be noted, Ocean’s Eleven-esque heists happen only in the movies.
Untapped Potential
Even though early forms of cloud computing can be traced back as far as the 1960s, the concept really only started to gain mainstream traction this century, with the launch of Amazon’s Simple Storage Service (S3) in 2006.
From that point on, things ramped up quickly. it didn’t take long for IT giants like Google, Microsoft, and Cisco to get in on the action with offerings of their own by 2008. In 2014, an IDG Enterprise study meant to estimate the extent to which the cloud has permeated into corporate consciousness reported that 69% of respondents “have at least one application or a portion of their computing infrastructure in the cloud.”
To illustrate how long it’s taken for big pharma to catch on, one of the earliest adopters within the industry, Pfizer, had been developing an online clinical trial system back in 2013, but ultimately abandoned the project. The silver lining of that cloud, though? The experience exposed Pfizer to the medium’s massive untapped potential and the firm has since revisited it.
The industry-wide shift is now well underway, signaled by the full-court press mounted by software vendors who have been developing cloud-based solutions for specific use within pharma. It’s hard to dispute the advantages firms would be foregoing by holding out any longer.
SaaS: Software as a Solution
For instance, regarding that scalable IT infrastructure, the cloud helps make pay-as-you-go Software-as-a-Service (SaaS) applications both affordable and accessible anywhere… on virtually any device. These include web-enabled or web-based options, with the former being beneficial to firms seeking to provide remote access to legacy applications. Applications that make up the latter are characterized by lower deployment costs and access directly via the web, with one potential drawback being the pre-requisite enterprise-wide standardization of browsers.
Software solutions exist for everything any pharmaceutical company could want or need, providing means to mine massive amounts of data for the purposes of drug research, for one example. For another, automated quality control platforms like GlobalVision positively impact ROI by minimizing the amount of unnecessary recalls due to packaging errors.
Featuring a (Mac or PC) desktop deployment option as well, GlobalVision is the first solution of its kind to take to the cloud, effectively embracing what has become an undeniable trend in computing in general, and, now, pharma by all accounts.
It’s admittedly only recently that pharma has come to take its seat at the table and it may be somewhat of a gamble, but that would be the case no matter the game. It just so happens that, in this one, most everyone wins.
GlobalVision is the leading developer of proofreading technologies for pharmaceutical packaging. Learn how GlobalVision has helped top Pharmaceutical Companies in quality control.
Request a free trial for GlobalVision Digital Inspection Solution
How More about How Error-Detection Software Ensures Data Integrity
6 Tips for Creating Error-Free Packaging
Date: March, 2017 | Category: Proofreading | Author: Jonathan Hou
Mastering Print Inspection for Your Business
Creating error-free packaging is a daunting task. With so many parties involved from brands, marketing agencies, pre-press, and print suppliers, ensuring no errors in packaging go by can be challenging.
We’ve compiled a list of industry best practices that you can use as a checklist to avoid errors getting through your printing process.
There are many different components involved when creating packaging, from the copy to the graphics, barcodes, and braille. To help ensure that you create error-free packaging and reduce the risk of dealing with a product recall, it’s always helpful to implement some best practices to follow.
Packaging Proofreading Starts With Up-to-Date PDFs
Most times when proofreading packaging, the PDF can go through many revisions before getting approved. Files can also be stored across different network shares or even on someone’s local computer. It’s key to ensure you know where to find the most up-to-date PDF. By doing so, you will avoid sending the wrong PDF to print!
Check Barcodes Early
It’s common for graphic artists to put placeholders for barcodes to show where the final barcodes will be positioned on the final packaging. You may notice the FPO symbol on top of a barcode which stands for “For Position Only.” We’ve seen this get missed when the print runs, meaning the correct barcode won’t appear.
It’s recommended to check the barcodes on your proofs, which can be done with software for checking barcodes or printing out the proofs and using a handheld verifier.
Proofreading the Printer’s Proof Prior to Approval
It’s easy enough to give a quick glance over your packaging artwork and tell your printer to go ahead with the job, but you really have to spend enough time to make sure there are no mistakes.
Make sure that either you or the customer service representative conduct thorough proofreading of files to check for errors in spelling, color, barcodes, and other content on the proof. One way to do this type of check is to do a line-by-line visual comparison.
Standardize Design Tools
Do you know what versions of Adobe Illustrator your suppliers are using? Chances are they are all using different versions. A different version of software equals different functionality and feature sets. Ensuring everyone is on the same version means everyone is talking the same language and you have repeatable results. You also know there won’t be any unintended changes due to the software you’re using.
Checking for the Right Products in a Job
Often to save costs, a printer may mix different products in a print job. Mixing products has the benefits of allowing better use of inks and reducing wasted material. However, it can also cause a risk of printing the wrong products.
If you are printing these “gang runs” make sure each product is accounted for on the press sheet to ensure you aren’t missing or adding any additional products to the print run.
Continuous Quality and Improvement
Continuous testing in software is the new approach when developing products. Most software products today will have some level of automated testing completed to check against expected results. This helps to continuously test code and ensure quality throughout the development process.
There’s no reason why this methodology can’t be applied to packaging development. Using tools to perform routine tasks like preflight and PDF compare can enable you to automate on a continuous basis to catch errors in packaging and files early on before you release.
By implementing these best practices, you will see an immediate reduction in errors and an overall improvement in quality. Delivering error-free prints will also increase your client’s confidence in your process and your own!
GlobalVision is the leading developer of proofreading technologies for print and packaging companies. Learn how GlobalVision can catch any deviations between version changes using Graphics Inspection Software.
Request a free trial for GlobalVision Graphics Inspection Solution
Learn More about Why Labeling Is a Must for Error-Free Packaging
The GlobalVision Platform has Transformed and it’s No Mistake
At GlobalVision, we understand the importance of aiming for perfection. With so much competition across endless industries, one slip up could mean the difference between the success or failure of a business’s quarter for the business.
All that pressure and resulting stress doesn’t do anyone any good. Knowing that we have the power to not only help clients improve the efficiency of their businesses but also to focus on more important things inspires us to push forward.
Each day we think to ourselves, “How can we improve, how can we do better so our customers can as well?”
That type of thinking is what caused us to recently get inspired, look inward, seek client feedback and revolutionize our existing products.
Introducing the New and Unified GlobalVision
For decades, GlobalVision has helped companies detect errors sooner and more consistently. We’ve preserved the integrity of brand images day in and day out, but knew that what we were doing could be better.
After countless late nights and weekends of diligent work, we’ve combined the entire suite of GlobalVision technologies into a single, unified platform for desktop deployments. Now, our clients can protect the quality and legitimacy of their businesses right from a desktop computer. Why does any of this matter to you?
Let’s take a closer look.
Efficiency, efficiency, efficiency
Some of our existing and prospective clients may be thinking, “Our process of proofing files with GlobalVision software worked seamlessly before. Why change it?” Well, there was a time we also thought it was efficient to use multiple applications to find inconsistencies.
With the unification of our software into one application, we’re trimming away unnecessary steps needed to ensure best-in-class quality inspection. Simply by reducing time spent switching between separate applications, employees can rapidly increase their productivity and as a result, revenue and profit for their companies.
As they say, time is money.
Here Are Some Other Ways We Have Made The New GlobalVision Platform Better:
As you can see, the GlobalVision team has been hard at work. Each of these updates was painstakingly thought through with the productivity of our clients in mind. And while the software is new, the same intuitive user interface hasn’t gone anywhere. At its core, it’s still the same quality control platform you know and love. We hope you’re as excited as we are about this monumental product launch!
GlobalVision is the leading developer of proofreading technologies for retail and consumer packaged goods. Learn how GlobalVision has helped Consumer Goods companies of all sizes in quality control.
Request a free trial for GlobalVision Graphics Inspection Solution.
Learn More about How to Reduce Your Carbon Footprint by Going Beyond Sustainable Packaging
12 Ways to Reduce Data Integrity Risks for Regulated Industries
Date: December, 2016 | Category: Quality | Author: Mike Malz
What Does Data Integrity Mean?
Data integrity refers to the fact that data must be reliable and accurate over its entire lifecycle. Data integrity and data security go hand in hand, even though they’re separate concepts. Uncorrupted data (integrity) is considered to be whole and then stays unchanged relative to that complete state.
It is important to understand what data integrity really means in order to be compliant.
Maintaining or keeping data consistent throughout its lifecycle is a matter of protecting it (security) so that it’s reliable. And data that’s reliable is simply able to meet certain standards, with which compliance is necessary. For example, the FDA uses the acronym ALCOA to define data integrity standards and to relate to good manufacturing practices.
Data Integrity Best Practices:
Data is expected to be:
The Importance of Data Integrity
Why is data integrity important?
Data integrity has become a serious issue over the past few years and therefore is a core focus of many enterprises. The FDA published a Data Integrity Guidance Document outlining compliance with CGMP that addresses the role of data integrity for the industry.
The document is a result of the FDA increasingly observing violations involving data integrity during inspections. These violations have led to FDA warning letters, import alerts, and consent decrees. The guidance document answers integrity questions and strives to clarify what the FDA expects from businesses.
How can Data Integrity Risks be Minimized?
In today’s marketplace, companies need to feel confident that there is no loss of quality when using computer systems. To accomplish this, there are effective strategies that companies may implement to manage their data integrity risks and ensure their data respects the ALCOA principle. By moving from a reactive to a proactive way of thinking, the following key requirements and controls may be put in place to ensure data integrity and minimize risk for your organization.
12 Ways to Reduce Data Integrity Risk:
1. Ensure all computer systems are 21 CFR Part 11 compliant
21 CFR Part 11 is an FDA regulation that applies to electronic records. It is required to ensure that electronic records are trustworthy, reliable, and equivalent to paper records. All computer systems that store data used to make quality decisions must be compliant, making it a perfect place to start with data integrity.
2. Follow a software development lifecycle
A Software Development Lifecycle methodology helps oversee that quality-related tasks are performed to address pertinent lifecycle phases from software development, software testing, integration, and installation to ongoing system maintenance. All computer systems should be appropriately developed, qualified, tested, and assessed on a regular basis.
3. Validate your computer systems
Software validation provides documented evidence to deliver assurance that a specific process consistently produces a product that meets its pre-determined specifications and quality attributes. To ensure your system can be validated, it is key to work with vendors that provide validation.
4. Implement audit trails
A secure, computer-generated, time-stamped audit trail records the identity, date, and time of data entries, changes, and deletions. Audit trails ensure the trustworthiness of the electronic record, demonstrate necessary data ownership, and assure records have not been modified or deleted.
5. Implement error detection software
Automated inspection software can help verify important documents to ensure their accuracy. Manual proofreading or inspections are proven to be inefficient and often cannot assure that files are error-free.
6. Secure your records with limited system access
All systems should require a login with at least two unique pieces of information and provide access only to required individuals to guarantee data integrity.
7. Maintain backup and recovery procedures
A backup and recovery strategy is necessary in the unexpected event of data loss and application errors. This procedure ensures the reconstruction of data is achieved through media recovery and the restoration of both physical and logical data and creates a safeguard to protect the integrity of your database files.
8. Design a Quality Management System with SOPs and logical controls
A Quality Management System with Standard Operating Procedures builds quality into the process by systematically controlling the process. It is essential to write and follow good effective procedures to ensure clear accountability.
9. Protect the physical and logical security of systems
Controls are needed to protect the physical and logical security of your systems, change management, service management, and system continuity. This will assure continuous development for your organization and support of systems.
10. Establish a vendor management qualification program
It is important to evaluate all vendors supplying products to certify that the products are quality products that meet needs (such as validation services). A continuous appraisal is required following the initial evaluation. Often asking what data integrity procedures your vendors have in place will help with your own organization’s data integrity practices.
11. Properly train users and maintain training records
Users should be properly trained so that they have the right education and expertise to perform their job competently. Documented training records provide this proof.
12. Conduct Internal Audits to evaluate controls and procedures
Internal audits ensure that all procedures are followed and that continuous improvement is emphasized.
Data Integrity Success
If you are reading this article, you are most probably aware of how important it is to ensure your data is not compromised. The impact of dangerous data can have resounding consequences on any organization no matter the size. However, if data integrity is thought of as a process, the data infrastructure can become an asset instead of a liability.
GlobalVision is the leading developer of automated quality control technologies for
every stage of the pharmaceutical workflow. Learn how GlobalVision has helped top Pharmaceutical Companies in quality control.
Request a free trial for GlobalVision Automated Proofreading Solution
Related Articles:
What is QMS? Quality Management System?
Software Development & Data Integrity