Date: May, 2017 | Category: Company | Author: Jonathan Hou
You see the words “web,” “cloud,” and “internet of things” just about everywhere you go these days. In today’s digital age, where “there’s an app” for almost everything, you probably wouldn’t last even 10 minutes without hearing something about the internet.
But how could you not, when technology has become an integral part of our everyday lives.
With the mainstream accessibility of broadband Internet and 4G, users can access their favorite web-based and mobile applications wherever and whenever they want. However, not all applications are created equal and the convenience afforded by the internet has different levels attached to it. Other factors like affordability and security considerations appear at the forefront of the ongoing debate between web-enabled and web-based applications.
Web- Enabled Vs. Web-Based
Web-Enabled
There is an inherent advantage to this approach. IT departments can provide employees with remote access to older, legacy programs to maximize the return on investment on specialized applications deployed across the company.
Those same applications may be firmly entrenched within the organization as key components, mission-critical to its processes and subsequent successes.
That ROI takes a hit though with added costs of maintaining a whole Citrix environment, not to mention all the extra network bandwidth usage from streaming video-like graphics across the web.
Often, it requires a client plug-in (ActiveX) control to be installed in the background. Plus, integration with web-based systems remains limited because the program in question is still just a desktop application, after all… albeit with extra layers tacked on to enable functionality over the internet.
There are also security risks with incorrectly implemented Citrix servers; Since remote desktop access to Citrix servers requires different permission levels for different users, there is the potential for unauthorized access to certain files on a Microsoft Windows file server.
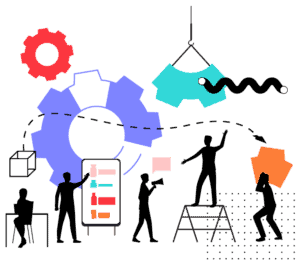
Web-Based
Meanwhile, one disadvantage is the required standardization of browsers across the company to ensure a consistent user experience. Another is the web in general to ensure a user experience, to begin with. Whereas web-enabled applications are based on desktop versions, web-based applications are based on, well, you guessed it, the internet! If the internet goes down, so too does the app.
That being said, a functioning internet connection is pretty much a prerequisite to running a business these days, and web-based applications are generally considered to be more cost-effective relative to their web-enabled cousins, as the application runs directly in a browser.
Furthermore, the applications themselves only need to be installed and updated on a single host server instead of on each workstation, which also means tighter security, and not having to focus on countless systems (as far as the single application is concerned).
Web-based applications can be hosted by the vendor, as in the classic Software-as-a-Service model, or the client, with several potential arrangements out there. This plays further into the notion that the web-based approach benefits from superior flexibility. Up-front and subscription-based pay schemes exist (although, in terms of hard cash doled out, both tend to even out over time).
Another advantage is that web-based applications can integrate near-seamlessly with the vast ecosystem of other web apps such as Salesforce CRM, Documentum, and cloud-based storage because they are cut from the same technological cloth.
With the growing trend of mobile devices being used as means to access apps remotely, research firm Gartner declared heading into 2015 that cloud and mobile computing will keep on converging, promoting the development of centralized applications for use anywhere. That sounds awful like a bet on “web-based” moving forward. A few years later, nothing has dispelled the argument that it’s more of a future-proof option… if you’re in the position to have an option between the two, anyway.
For more information on this constant debate, please visit:
→ Web-Based Vs. Web-Enabled Software
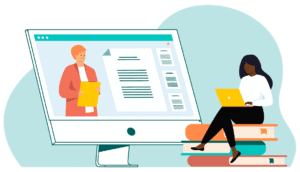
Which Application is Better?
Sticking with the mobile device example, deciding between a web-enabled application and a web-based application is like deciding between smart and flip phones. Both can make calls, but you gain access to a much larger ecosystem of integrated apps with your smartphone’s newer technology.
Everything may be headed in the same direction, and web-enabled and web-based applications each take you from Point A to Point B. However, it’s Points C-Z that are the issue. Roads are opening up as we speak and a trusty 18-wheeler representing web-enabled applications might not be able to fit through tunnels out of town. Not like a sleek, mobile-device-friendly sedan anyway.
GlobalVision however, offers both versions of its market-leading automated proofreading technology.
For those who prefer their desktop application, there’s GlobalVision Desktop (GVD). Built for use in production environments, GVD combines powerful inspection tools into one robust application – so you can be sure your files are accurate as they move along the quality workflow.
However, for those who prefer to work on a cloud, web-based application, our latest and most innovative proofreading technology Verify is just for you.
Created for regulated industries, Verify is GlobalVision’s inspection technology reinvented. Verify ensures a seamless and convenient end-user experience, delivering superior inspection results, in a cloud-based, innovative software.
Learn more by requesting a demo of GlobalVision here or try our web-based proofreading software, Verify, for free!
GlobalVision is the leading developer of quality control technologies. Learn how GlobalVision has provided new business opportunities across all industries with an extra layer of security.
Request a free trial for GlobalVision Digital Inspection Solution
Learn More about the Actual Difference Between Quality Control Inspection Apps
Why “Web-Enabled” Apps Aren’t Really Web Apps
Date: May, 2017 | Category: Company | Author: Jonathan Hou
You see the words “web,” “cloud,” and “internet of things” just about everywhere you go these days. In today’s digital age, where “there’s an app” for almost everything, you probably wouldn’t last even 10 minutes without hearing something about the internet.
But how could you not, when technology has become an integral part of our everyday lives.
With the mainstream accessibility of broadband Internet and 4G, users can access their favorite web-based and mobile applications wherever and whenever they want. However, not all applications are created equal and the convenience afforded by the internet has different levels attached to it. Other factors like affordability and security considerations appear at the forefront of the ongoing debate between web-enabled and web-based applications.
Web- Enabled Vs. Web-Based
Web-Enabled
There is an inherent advantage to this approach. IT departments can provide employees with remote access to older, legacy programs to maximize the return on investment on specialized applications deployed across the company.
Those same applications may be firmly entrenched within the organization as key components, mission-critical to its processes and subsequent successes.
That ROI takes a hit though with added costs of maintaining a whole Citrix environment, not to mention all the extra network bandwidth usage from streaming video-like graphics across the web.
Often, it requires a client plug-in (ActiveX) control to be installed in the background. Plus, integration with web-based systems remains limited because the program in question is still just a desktop application, after all… albeit with extra layers tacked on to enable functionality over the internet.
There are also security risks with incorrectly implemented Citrix servers; Since remote desktop access to Citrix servers requires different permission levels for different users, there is the potential for unauthorized access to certain files on a Microsoft Windows file server.
Web-Based
Meanwhile, one disadvantage is the required standardization of browsers across the company to ensure a consistent user experience. Another is the web in general to ensure a user experience, to begin with. Whereas web-enabled applications are based on desktop versions, web-based applications are based on, well, you guessed it, the internet! If the internet goes down, so too does the app.
That being said, a functioning internet connection is pretty much a prerequisite to running a business these days, and web-based applications are generally considered to be more cost-effective relative to their web-enabled cousins, as the application runs directly in a browser.
Furthermore, the applications themselves only need to be installed and updated on a single host server instead of on each workstation, which also means tighter security, and not having to focus on countless systems (as far as the single application is concerned).
Web-based applications can be hosted by the vendor, as in the classic Software-as-a-Service model, or the client, with several potential arrangements out there. This plays further into the notion that the web-based approach benefits from superior flexibility. Up-front and subscription-based pay schemes exist (although, in terms of hard cash doled out, both tend to even out over time).
Another advantage is that web-based applications can integrate near-seamlessly with the vast ecosystem of other web apps such as Salesforce CRM, Documentum, and cloud-based storage because they are cut from the same technological cloth.
With the growing trend of mobile devices being used as means to access apps remotely, research firm Gartner declared heading into 2015 that cloud and mobile computing will keep on converging, promoting the development of centralized applications for use anywhere. That sounds awful like a bet on “web-based” moving forward. A few years later, nothing has dispelled the argument that it’s more of a future-proof option… if you’re in the position to have an option between the two, anyway.
For more information on this constant debate, please visit:
→ Web-Based Vs. Web-Enabled Software
Which Application is Better?
Sticking with the mobile device example, deciding between a web-enabled application and a web-based application is like deciding between smart and flip phones. Both can make calls, but you gain access to a much larger ecosystem of integrated apps with your smartphone’s newer technology.
Everything may be headed in the same direction, and web-enabled and web-based applications each take you from Point A to Point B. However, it’s Points C-Z that are the issue. Roads are opening up as we speak and a trusty 18-wheeler representing web-enabled applications might not be able to fit through tunnels out of town. Not like a sleek, mobile-device-friendly sedan anyway.
GlobalVision however, offers both versions of its market-leading automated proofreading technology.
For those who prefer their desktop application, there’s GlobalVision Desktop (GVD). Built for use in production environments, GVD combines powerful inspection tools into one robust application – so you can be sure your files are accurate as they move along the quality workflow.
However, for those who prefer to work on a cloud, web-based application, our latest and most innovative proofreading technology Verify is just for you.
Created for regulated industries, Verify is GlobalVision’s inspection technology reinvented. Verify ensures a seamless and convenient end-user experience, delivering superior inspection results, in a cloud-based, innovative software.
Learn more by requesting a demo of GlobalVision here or try our web-based proofreading software, Verify, for free!
GlobalVision is the leading developer of quality control technologies. Learn how GlobalVision has provided new business opportunities across all industries with an extra layer of security.
Request a free trial for GlobalVision Digital Inspection Solution
Learn More about the Actual Difference Between Quality Control Inspection Apps
How a Little Error Can Ruin a Great Design
Our world is growing at a rapid pace and so is the consumer market. The space between the market and the consumer’s home has drastically shrunk in the recent times, with online marketplaces as the next big thing. Customers can easily book, order and buy different items from all around the world—and get it delivered directly to their homes.
In such a crowded space what do you think catches the eye of your target audience?
Well, these are a few factors that influence a person to buy your product. And that is why, as a designer, you must try vigilantly to avoid little errors—because those small mistakes can ruin a great design and an amazing product.
A few design errors, like the following, can ruin an otherwise well-made design:
Not Understanding the Product and the Target Audience
This often happens when different teams handle various aspects of the development of the product. And more than often it happens that the designing team doesn’t fully understand the product, so the end design doesn’t fully or properly convey the product to the target audience.
Way back in 1997, the now famous animation cartoon The Pokemon was banned after 700 children around Japan suffered from various ailments. Some of the children experienced blurred vision, a few passed out and many complained of nausea. Some extreme cases were reported where the children suffered seizures and temporary blindness.
What caused all this?
Well, in the episode called “Electric Soldier Porygon” there was a scene where Pokemon strikes lightning, and the screen goes all blue and red for some time. This lightning effect triggered “photosensitive seizures” in the children, and one in every four thousand children suffers.
The episode was banned and was never broadcasted anywhere in the world again.
How can designers avoid such mistakes?
Designers must have knowledge of the product as well as the target audience, and and what might trigger a negative or positive behavior in them. For example—simple understanding of color psychology would have prevented The Pokemon episode ban entirely.
Using the Wrong Typography and Font Overload
Designers always play with fonts and typography, and font design and size are one of the most important parts of any print or online media. The key is to maintain the perfect balance and not overdo it.
A design is not about arranging pretty looking fonts and merely being pleasing the eye of the consumer; it’s also important to grab their attention and speaking directly to them. Any fonts used in a design must blend well with not only the background but the overall message the brand wants to deliver.
Check out some of the top fonts for packaging design.
Not Saving Files in the Correct Format
Amateurs might not have much experience or professional training, but companies often hire them to create designs in order to save some money. But what many beginners fail to remember is that saving files in the correct format is as essential as the design itself.
Usually, most of the print work is saved in CMYK format with 300 dpi, and most of the web work has to be saved in RGB. If not saved in the correct format then the final print might not be as clear as expected, and in turn it can end up ruining all your printed material.
Readability and Spellings
Let’s understand one thing here: designers are not copywriters. They mess up spellings and misuse words. To avoid these types of mistakes, proofread all the documents—and the best way to proofread can be to use proofreading software or spelling inspection tools.
You can also avoid readability problems and spelling errors by asking someone else read it or hiring a professional. A fresh eye will always catch more errors than the designer can.
These were some of the errors that commonly occur and can be avoided easily. And while they might seem harmless, if these mistakes are not taken care of early on then it might ruin the finished design completely. In a time when consumers crave impeccably-designed products and want to stay constantly updated with the latest offering in the market, a miniscule error can not only ruin your design but also hurt your sales.
Guest post by Marvin Magursara,
SEO Manager, GlobalVision
Marvin Magusara studied Robotics Engineering at UWE Bristol and is currently an SEO manager at GlobalVision, a company that provides machine vision software technology for quality control in packaging inspection.
His speciality field of Digital Marketing is SEO. He is currently working as an SEO consultant for a variety of companies.
Marvin is also an entrepreneur; he’s the founder of Graftene, a Web Agency and BubbleLocal SEO.
Due to his obsession with SEO, he spends most of his working hours doing SEO and content marketing, and writing for notable blogs in the marketing sphere.
GlobalVision is the leading developer of proofreading technologies for retail and consumer packaged goods. Learn how GlobalVision has helped Consumer Goods companies of all sizes in quality control.
Request a free trial for GlobalVision Digital Inspection Solution
Learn More about How Can Printed Manuals Improve Your Staff Training
Big Pharma Pokes Its Head in the Cloud (Finally)
Known for keeping their cards close to their vests to prevent other players from sneaking a peek, drug companies waited until the last possible moment to move to the cloud. Now sufficiently satisfied that their security concerns have been addressed, they’re finally poised to reap the benefits.
Positive Side-Effects
The advantages the cloud offers are wide-ranging. They run the gamut from facilitated corporate communication between teams in different parts of the world to lower operational costs, both of which are to be expected to a certain extent. They are arguably even interconnected as increased collaboration can help lead to streamlined operations.
However, other benefits aren’t as obvious. These include the flexibility of a scalable IT infrastructure (we’ll get to that later on), and, yes, even increased security. That would be through a variety of measures like encryption, cloud data protection gateways, and hybrid setups, which allow companies to store confidential data on private clouds.
Security concerns within the industry were in part due to required compliance with laws and regulations such as those enacted by the Health Insurance Portability Act. They’re also in part due to best practices, which logically state that sensitive, proprietary information should be protected much like cubs would be by a grizzly bear.
However, as has long been established, if done right, cybersecurity should present no more of an issue than implementing proper physical security measures would in the real world. There is a natural apprehension to deviate from what has been the norm for decades, but the reality is the cloud can be more secure than a brick-and-mortar fortress of a casino, and, it should be noted, Ocean’s Eleven-esque heists happen only in the movies.
Untapped Potential
Even though early forms of cloud computing can be traced back as far as the 1960s, the concept really only started to gain mainstream traction this century, with the launch of Amazon’s Simple Storage Service (S3) in 2006.
From that point on, things ramped up quickly. it didn’t take long for IT giants like Google, Microsoft, and Cisco to get in on the action with offerings of their own by 2008. In 2014, an IDG Enterprise study meant to estimate the extent to which the cloud has permeated into corporate consciousness reported that 69% of respondents “have at least one application or a portion of their computing infrastructure in the cloud.”
To illustrate how long it’s taken for big pharma to catch on, one of the earliest adopters within the industry, Pfizer, had been developing an online clinical trial system back in 2013, but ultimately abandoned the project. The silver lining of that cloud, though? The experience exposed Pfizer to the medium’s massive untapped potential and the firm has since revisited it.
The industry-wide shift is now well underway, signaled by the full-court press mounted by software vendors who have been developing cloud-based solutions for specific use within pharma. It’s hard to dispute the advantages firms would be foregoing by holding out any longer.
SaaS: Software as a Solution
For instance, regarding that scalable IT infrastructure, the cloud helps make pay-as-you-go Software-as-a-Service (SaaS) applications both affordable and accessible anywhere… on virtually any device. These include web-enabled or web-based options, with the former being beneficial to firms seeking to provide remote access to legacy applications. Applications that make up the latter are characterized by lower deployment costs and access directly via the web, with one potential drawback being the pre-requisite enterprise-wide standardization of browsers.
Software solutions exist for everything any pharmaceutical company could want or need, providing means to mine massive amounts of data for the purposes of drug research, for one example. For another, automated quality control platforms like GlobalVision positively impact ROI by minimizing the amount of unnecessary recalls due to packaging errors.
Featuring a (Mac or PC) desktop deployment option as well, GlobalVision is the first solution of its kind to take to the cloud, effectively embracing what has become an undeniable trend in computing in general, and, now, pharma by all accounts.
It’s admittedly only recently that pharma has come to take its seat at the table and it may be somewhat of a gamble, but that would be the case no matter the game. It just so happens that, in this one, most everyone wins.
GlobalVision is the leading developer of proofreading technologies for pharmaceutical packaging. Learn how GlobalVision has helped top Pharmaceutical Companies in quality control.
Request a free trial for GlobalVision Digital Inspection Solution
How More about How Error-Detection Software Ensures Data Integrity
6 Tips for Creating Error-Free Packaging
Date: March, 2017 | Category: Proofreading | Author: Jonathan Hou
Mastering Print Inspection for Your Business
Creating error-free packaging is a daunting task. With so many parties involved from brands, marketing agencies, pre-press, and print suppliers, ensuring no errors in packaging go by can be challenging.
We’ve compiled a list of industry best practices that you can use as a checklist to avoid errors getting through your printing process.
There are many different components involved when creating packaging, from the copy to the graphics, barcodes, and braille. To help ensure that you create error-free packaging and reduce the risk of dealing with a product recall, it’s always helpful to implement some best practices to follow.
Packaging Proofreading Starts With Up-to-Date PDFs
Most times when proofreading packaging, the PDF can go through many revisions before getting approved. Files can also be stored across different network shares or even on someone’s local computer. It’s key to ensure you know where to find the most up-to-date PDF. By doing so, you will avoid sending the wrong PDF to print!
Check Barcodes Early
It’s common for graphic artists to put placeholders for barcodes to show where the final barcodes will be positioned on the final packaging. You may notice the FPO symbol on top of a barcode which stands for “For Position Only.” We’ve seen this get missed when the print runs, meaning the correct barcode won’t appear.
It’s recommended to check the barcodes on your proofs, which can be done with software for checking barcodes or printing out the proofs and using a handheld verifier.
Proofreading the Printer’s Proof Prior to Approval
It’s easy enough to give a quick glance over your packaging artwork and tell your printer to go ahead with the job, but you really have to spend enough time to make sure there are no mistakes.
Make sure that either you or the customer service representative conduct thorough proofreading of files to check for errors in spelling, color, barcodes, and other content on the proof. One way to do this type of check is to do a line-by-line visual comparison.
Standardize Design Tools
Do you know what versions of Adobe Illustrator your suppliers are using? Chances are they are all using different versions. A different version of software equals different functionality and feature sets. Ensuring everyone is on the same version means everyone is talking the same language and you have repeatable results. You also know there won’t be any unintended changes due to the software you’re using.
Checking for the Right Products in a Job
Often to save costs, a printer may mix different products in a print job. Mixing products has the benefits of allowing better use of inks and reducing wasted material. However, it can also cause a risk of printing the wrong products.
If you are printing these “gang runs” make sure each product is accounted for on the press sheet to ensure you aren’t missing or adding any additional products to the print run.
Continuous Quality and Improvement
Continuous testing in software is the new approach when developing products. Most software products today will have some level of automated testing completed to check against expected results. This helps to continuously test code and ensure quality throughout the development process.
There’s no reason why this methodology can’t be applied to packaging development. Using tools to perform routine tasks like preflight and PDF compare can enable you to automate on a continuous basis to catch errors in packaging and files early on before you release.
By implementing these best practices, you will see an immediate reduction in errors and an overall improvement in quality. Delivering error-free prints will also increase your client’s confidence in your process and your own!
GlobalVision is the leading developer of proofreading technologies for print and packaging companies. Learn how GlobalVision can catch any deviations between version changes using Graphics Inspection Software.
Request a free trial for GlobalVision Graphics Inspection Solution
Learn More about Why Labeling Is a Must for Error-Free Packaging
The GlobalVision Platform has Transformed and it’s No Mistake
At GlobalVision, we understand the importance of aiming for perfection. With so much competition across endless industries, one slip up could mean the difference between the success or failure of a business’s quarter for the business.
All that pressure and resulting stress doesn’t do anyone any good. Knowing that we have the power to not only help clients improve the efficiency of their businesses but also to focus on more important things inspires us to push forward.
Each day we think to ourselves, “How can we improve, how can we do better so our customers can as well?”
That type of thinking is what caused us to recently get inspired, look inward, seek client feedback and revolutionize our existing products.
Introducing the New and Unified GlobalVision
For decades, GlobalVision has helped companies detect errors sooner and more consistently. We’ve preserved the integrity of brand images day in and day out, but knew that what we were doing could be better.
After countless late nights and weekends of diligent work, we’ve combined the entire suite of GlobalVision technologies into a single, unified platform for desktop deployments. Now, our clients can protect the quality and legitimacy of their businesses right from a desktop computer. Why does any of this matter to you?
Let’s take a closer look.
Efficiency, efficiency, efficiency
Some of our existing and prospective clients may be thinking, “Our process of proofing files with GlobalVision software worked seamlessly before. Why change it?” Well, there was a time we also thought it was efficient to use multiple applications to find inconsistencies.
With the unification of our software into one application, we’re trimming away unnecessary steps needed to ensure best-in-class quality inspection. Simply by reducing time spent switching between separate applications, employees can rapidly increase their productivity and as a result, revenue and profit for their companies.
As they say, time is money.
Here Are Some Other Ways We Have Made The New GlobalVision Platform Better:
As you can see, the GlobalVision team has been hard at work. Each of these updates was painstakingly thought through with the productivity of our clients in mind. And while the software is new, the same intuitive user interface hasn’t gone anywhere. At its core, it’s still the same quality control platform you know and love. We hope you’re as excited as we are about this monumental product launch!
GlobalVision is the leading developer of proofreading technologies for retail and consumer packaged goods. Learn how GlobalVision has helped Consumer Goods companies of all sizes in quality control.
Request a free trial for GlobalVision Graphics Inspection Solution.
Learn More about How to Reduce Your Carbon Footprint by Going Beyond Sustainable Packaging
12 Ways to Reduce Data Integrity Risks for Regulated Industries
Date: December, 2016 | Category: Quality | Author: Mike Malz
What Does Data Integrity Mean?
Data integrity refers to the fact that data must be reliable and accurate over its entire lifecycle. Data integrity and data security go hand in hand, even though they’re separate concepts. Uncorrupted data (integrity) is considered to be whole and then stays unchanged relative to that complete state.
It is important to understand what data integrity really means in order to be compliant.
Maintaining or keeping data consistent throughout its lifecycle is a matter of protecting it (security) so that it’s reliable. And data that’s reliable is simply able to meet certain standards, with which compliance is necessary. For example, the FDA uses the acronym ALCOA to define data integrity standards and to relate to good manufacturing practices.
Data Integrity Best Practices:
Data is expected to be:
The Importance of Data Integrity
Why is data integrity important?
Data integrity has become a serious issue over the past few years and therefore is a core focus of many enterprises. The FDA published a Data Integrity Guidance Document outlining compliance with CGMP that addresses the role of data integrity for the industry.
The document is a result of the FDA increasingly observing violations involving data integrity during inspections. These violations have led to FDA warning letters, import alerts, and consent decrees. The guidance document answers integrity questions and strives to clarify what the FDA expects from businesses.
How can Data Integrity Risks be Minimized?
In today’s marketplace, companies need to feel confident that there is no loss of quality when using computer systems. To accomplish this, there are effective strategies that companies may implement to manage their data integrity risks and ensure their data respects the ALCOA principle. By moving from a reactive to a proactive way of thinking, the following key requirements and controls may be put in place to ensure data integrity and minimize risk for your organization.
12 Ways to Reduce Data Integrity Risk:
1. Ensure all computer systems are 21 CFR Part 11 compliant
21 CFR Part 11 is an FDA regulation that applies to electronic records. It is required to ensure that electronic records are trustworthy, reliable, and equivalent to paper records. All computer systems that store data used to make quality decisions must be compliant, making it a perfect place to start with data integrity.
2. Follow a software development lifecycle
A Software Development Lifecycle methodology helps oversee that quality-related tasks are performed to address pertinent lifecycle phases from software development, software testing, integration, and installation to ongoing system maintenance. All computer systems should be appropriately developed, qualified, tested, and assessed on a regular basis.
3. Validate your computer systems
Software validation provides documented evidence to deliver assurance that a specific process consistently produces a product that meets its pre-determined specifications and quality attributes. To ensure your system can be validated, it is key to work with vendors that provide validation.
4. Implement audit trails
A secure, computer-generated, time-stamped audit trail records the identity, date, and time of data entries, changes, and deletions. Audit trails ensure the trustworthiness of the electronic record, demonstrate necessary data ownership, and assure records have not been modified or deleted.
5. Implement error detection software
Automated inspection software can help verify important documents to ensure their accuracy. Manual proofreading or inspections are proven to be inefficient and often cannot assure that files are error-free.
6. Secure your records with limited system access
All systems should require a login with at least two unique pieces of information and provide access only to required individuals to guarantee data integrity.
7. Maintain backup and recovery procedures
A backup and recovery strategy is necessary in the unexpected event of data loss and application errors. This procedure ensures the reconstruction of data is achieved through media recovery and the restoration of both physical and logical data and creates a safeguard to protect the integrity of your database files.
8. Design a Quality Management System with SOPs and logical controls
A Quality Management System with Standard Operating Procedures builds quality into the process by systematically controlling the process. It is essential to write and follow good effective procedures to ensure clear accountability.
9. Protect the physical and logical security of systems
Controls are needed to protect the physical and logical security of your systems, change management, service management, and system continuity. This will assure continuous development for your organization and support of systems.
10. Establish a vendor management qualification program
It is important to evaluate all vendors supplying products to certify that the products are quality products that meet needs (such as validation services). A continuous appraisal is required following the initial evaluation. Often asking what data integrity procedures your vendors have in place will help with your own organization’s data integrity practices.
11. Properly train users and maintain training records
Users should be properly trained so that they have the right education and expertise to perform their job competently. Documented training records provide this proof.
12. Conduct Internal Audits to evaluate controls and procedures
Internal audits ensure that all procedures are followed and that continuous improvement is emphasized.
Data Integrity Success
If you are reading this article, you are most probably aware of how important it is to ensure your data is not compromised. The impact of dangerous data can have resounding consequences on any organization no matter the size. However, if data integrity is thought of as a process, the data infrastructure can become an asset instead of a liability.
GlobalVision is the leading developer of automated quality control technologies for
every stage of the pharmaceutical workflow. Learn how GlobalVision has helped top Pharmaceutical Companies in quality control.
Request a free trial for GlobalVision Automated Proofreading Solution
Related Articles:
What is QMS? Quality Management System?
Software Development & Data Integrity
Managing Barcodes in Packaging Quality Control
Every product in every store all over the world has a barcode on it.
As consumers, we cannot read barcodes, and really don’t care much about them.
We identify products by their name, by their color, by the brand name and logos.
However, barcodes are how brands and their entire worldwide supply chain manage the distribution, logistics, inventory, and point of sale, including discounts, pricing and returns.
Imagine you are at the checkout counter buying a jug of milk for $2.19.
What if the cashier scans the barcode of the milk jug and your bill said “Red Wine for $39.50”?
This is a barcode mix up.
You know the price for the jug of milk is $2.19, but the cash register doesn’t.
The store is very likely to return this product back to the distributor.
But not just this milk jug.
All the milk jugs in this store, and in all the warehouses everywhere.
The stores simply cannot sell them.
The barcode is a critical design element on the artwork.
Lets go a step further.
A barcode mixup is not the only potential issue.
“Why can’t the cashier scan the barcode at the checkout counter?”
What if we were back at the checkout counter, but this time it’s the right barcode, but it will not scan.
Again, the store is very likely to return this product back to the distributor.
The quality of every barcode, of every type, on every single product is critical to the successful sale of a product out in a fierce market place.
What do you need to look out for when it comes to Barcodes?
Misconception #4 -The Barcode, is part four in a five part series about the misconceptions in packaging quality control. Visit our blog next week for Misconception #5 – The Printed Component.
GlobalVision is the leading developer of proofreading technologies for retail and consumer packaged goods. Learn how GlobalVision has helped Consumer Goods companies of all sizes in quality control.
Request a free trial for GlobalVision Barcode Inspection Solution
Learn More about 10 Ways to Improve Your Barcodes
How to Know When a Printer’s Proof is Print-Ready
Date: October, 2016 | Category: Proofreading | Author: Reuben Malz
A brand company goes through many revision cycles until a final PDF is approved.
A typical cycle may look something like this; management gives the go-ahead to print 500,000 labels. Then, purchasing fires off a purchase order to the printer with the approved PDF file attached.
Most people consider this to be the end of the line and the expectation is that the printed labels will be delivered in a few days.
However, the packaging engineers know better. The Brand companies approved PDF is far from being “Print-Ready”.
How to Know When a Printer’s Proof is Print-Ready?
The Printer depends on professionals for many steps of the printing process. From pre-press to trap, bleeds, imposing the file, and correcting errors in the Brand company files, and much more. The end result is a derivative of the Brand company’s approved PDF file. This is the “Printer’s Proof”.
But Printing still cannot begin.
Remember the Purchase Order the Brand company sent to the Printer? This is the “Contract”.
In order for the printer to get paid for printing 500,000 labels, the contract requires that the 500,000 labels match the Brand company’s approved PDF file exactly, NOT the Proof!
Printing cannot begin until the PDF is verified against the Proof, but, whose responsibility is it to check the Proof?
The Importance of Verifying Print Proofs
Most printers will send the proof to the Brand company and wait for the signoff before starting print production.
But even with the Brand companies signoff of the proof, the printer cannot take the risk and assume there are no errors in the Proof for the following reasons:
The Brand company may sign and never have checked the Proof.
The Brand company may have checked quickly and missed an obvious error.
The responsibility is usually assumed to be shared.
The Purchase order has legal weight.
The Brand company may be in the wrong and refuse to pay.
The Brand company may be wrong, but the Printer will not want to lose the customer.
The Brand company may be in the right but loses time to market.
The Brand company may be in the right, but delays production.
It is for these reasons that both parties will need to verify the Printer’s Proof.
Additional Resources
GlobalVision is the leading developer of proofreading technologies for retail and consumer packaged goods. Learn how GlobalVision has helped Consumer Goods companies of all sizes in quality control.
For more information about GlobalVision and our market-leading Quality Control Platform for print and packaging, please visit our website or read more about the benefits of automated proofreading software on our blog.
Ready to make the switch and automate your quality control processes? Request a free trial for GlobalVision Print Inspection Solution.
Learn More about How to Create Error-Free Packagingby watching out video below.
Announcing GlobalVision Technologies Built into Esko Automation Engine
Forget 7. 16 is the next big thing.
This week marks the iPhone 7 launch but for us prepress folks, we’ve got something to be more excited about with the launch of Esko Software Platform 16. 16 marks the arrival of GlobalVision’s built-in technologies in Automation Engine. So what does it mean when two leading prepress software providers team up? The industry’s first fully automated quality control prepress workflow solution. Why is this a game changer? Just like Siri became a game changer with a smart personal assistant for your iPhone, GlobalVision is your smart QC assistant for Automation Engine. Don’t worry anymore about having to do manual comparisons on files, printing out files and checking barcodes or proofreading for spelling and text errors. Pass one or two files through GlobalVision and our QC assistant will tell you any problems related to your files.
Ask, “GlobalVision what’s wrong with my files?” and GlobalVision lets you know:
“You don’t have enough quiet zone in your barcode.” – Barproof | Barcode inspection
“You’ve spelled allergans wrong.”- Spellproof | Spelling inspection
“The text from your approved document was not found in your artwork.”- Docuproof | Text inspection
“The colors are different in your file.”- Artproof | Graphics inspection
“You’ve printed something that doesn’t match the PDF.”- Scanproof | Print inspection
“This is exactly what I hoped it would do”
Suddenly, QC becomes easy, and you can view GlobalVision’s inspection reports and decide if you want to pass the artwork onto production or have it reworked in prepress. Checking for text, color, barcode, even Braille errors has never been easier.
Used to seeing it in your Esko Viewer? Not a problem, GlobalVision results show up directly in Esko Viewer and even in Illustrator through Esko’s DeskPack plugins and even in WebCenter, for your customer portal.
Brand companies can benefit too with pre-defined checks for regulatory text approvals and text comparisons for nutrition facts. The most powerful piece of this puzzle is the ability for you to build custom workflows and design these automated checks in your Automation Engine workflow to the way your company works.
You can have your customers run an automated spellcheck before sending over their jobs to you or automatically find differences in your pre-press files vs. the customer’s artwork.
You can now build in rules when errors are found within Automation Engine but If everything is fine, just continue to the next step in the Automation Engine workflow and save your reports to view later.
With the ability to run inspection in parallel and in batches, you’ve just multiplied your QC and pre-press teams.
The feedback in talking with Pre-release customers for Automation Engine 16 over the last few months has just been fantastic with comments like “this is exactly what I hoped it would do” to “this is a game changer for the pre-press industry.”
Making our customers’ lives easier, more efficient and error free is what we strive to do here at GlobalVision, and I am proud to say the teaming up of Esko and GlobalVision does just that, making the last three years of joint development well worth it. That’s why I think 16 is the next big thing.
Learn how GlobalVision can help ensure data integrity using Automated Proofreading.
Request a free trial for GlobalVision Digital Inspection Solution
Learn More about How Esko Software Platform Makes Packaging Simplified
CMOs of Increasing Importance to Pharmaceutical Companies
Date: July, 2016 | Category: Compliance | Author: Reuben Malz
The pharmaceutical marketplace has changed dramatically over the last few years as pharmaceutical companies are moving from centralized, internal production to single-source providers or Contract Manufacturing Organizations (CMO).
The principal reason behind this evolution in the landscape is simple, to cut costs, increase capacity and reduce time-to-market. Beyond these obvious criteria, there are numerous other reasons why pharmaceutical companies are relying heavily on the growing CMO market.
Whereas CMOs once produced primary packaging they now offer a multitude of services from design and discovery to final packaging.
Outsourcing to a CMO allows the pharmaceutical company to add technical resources without increasing its overhead costs. The result of this is that the pharmaceutical company does not need to invest in expanding its staff and manufacturing facilities, to add new varieties of medicines into its product lines.
Pharmaceutical companies can now concentrate on core products regarding R&D and production and leave their secondary and tertiary products to the CMO.
CMOs of Increasing Importance to Pharmaceutical Companies
What is a CMO?
The term CMO can refer to a multitude of different companies including Contract Packaging Organizations, and Contract Pharmaceutical Manufacturers. However, in recent years CMOs have been more or less classified into two types of organizations:
API Contract Manufacturer (Active Pharmaceutical Ingredient)
These are companies that manufacture a substance(s) that are used as a component of a finished drug.
FDF Contract Manufacturer (Finished Dosage Form)
These are companies that provide a drug product for administration to a patient without the need for substantial further manufacturing and often in its final packaged form. The CMO market is currently divided almost equally between API manufacturers and FDF manufacturers.
Within FDF contract manufacturing, solid dose compounds currently dominate the market. However, future growth is likely to be driven by injectables dose manufacturing primarily due to an increased focus on complex disease areas and the growing trend of self-administration.
A Growing CMO Market
Regarding market growth and potential future growth, the CMO channel is a force to reckon with.
For North America, Europe, and Japan in the last years, the CMO market grew at close to three times the rate of the pharmaceutical market: 8% versus 3%.
(It is important to note that the 3% growth is for the pharmaceutical market as a whole, top Pharmaceutical companies have grown significantly faster at a rate average of over 11%. It is also important to note that most large pharmaceutical companies have divisions operating as CMO)
Over the next decade years, the CMO market is expected to continue to grow at an annual rate of 6% to 9%, with annual revenues currently valued at between 25-30 billion dollars. This growth will be further fueled by new opportunities within the generic drug market.
Challenges for the CMO
Although the CMO seems to be poised to become a major player in the pharmaceutical marketplace several challenges await.
Acquisitions
The trend is already apparent as 2015 saw a glut of companies and manufacturing facilities being bought and sold.
Current Clients
Smaller pharmaceutical companies use the services of CMOs significantly more than large pharmaceutical companies. The challenge lies in that the growth opportunities are a lot smaller.
Low Capital Costs
With lower capital costs many pharmaceutical companies are rethinking the CMO route for moving back to traditional centralized production.
The Future of CMOs
As with any part of the pharmaceutical landscape, the role of the CMO will follow a predictable route. Larger ones will absorb the smaller CMOs, and the large CMOs will come forward to be the only players to be able to support the large Pharmaceutical and Biopharmaceutical companies.
New channels will open within the generic pharmaceutical marketplace fostering further growth for the large CMO.
GlobalVision is the leading developer of proofreading technologies for the FDF Contract Manufacturer market. All our quality control solutions meet FDA 21 CFR Part 11 / EMA Annex 11 requirements.
For more information on GlobalVision and the Quality Control Platform for CMOs, please visit: globalvision.co or email: info@globalvision.co
Learn More about How to Ensure a Successful Printer-Pharma Relationship